Effect of Ball Mill Parameters' Variation on the Particles of a
The milling time can be considered in the derivation for future research direction. ... The equation can be used for the prediction of the effective particle size, mill-ball speed, and diameter (size) for the leaching process (optimal activation parameters for MA-assisted leaching sustainability). 5.
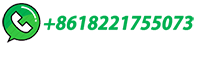