Crushers Selection Guide: Types, Features, Applications
Crushing devices hold feed material between two solid surfaces and apply sufficient force to fracture or deform that material. Primary crushing operations takes boulder size feeds (20 to 100 inches) and reduces the material to secondary crusher feed size (1 to 20 inches) or mill feed size (0.5 to 3 inches).
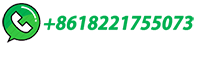