Pelletizing
Primetals Technologies and Outotec Oyj ( Outotec) have entered into an exclusive license agreement enabling Primetals Technologies to use straight grate iron ore pelletizing. 18.05.2021
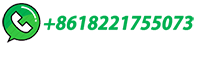
Primetals Technologies and Outotec Oyj ( Outotec) have entered into an exclusive license agreement enabling Primetals Technologies to use straight grate iron ore pelletizing. 18.05.2021
Outotec Digital Solutions for Iron Ore Pelletizing Plants provide a vital building block for the development of a state-of-the art plant that leverages our leading-edge digital technologies to ensure optimal operation and maintenance over the entire plant life cycle. Using our extensive experience as the original inventor of the ...
The ratio in the output from the three main pelletizing technologies changes depending on practical circumstances, such as iron ore reserves, iron ore types, market demand, and required investment. The ratio for grate-kiln pellets has increased to 55.33% in 2011 from 7.21% in 2000, while the ratio for shaft furnace pellets has dropped to 42.05% ...
pelletizing technologies have been developed and the production of fired pellets has ... straight grate systems are the dominant technologies currently being used in the iron ore pelletizing industry.
Pelletizing feed preparation and mixing: the raw material (iron ore concentrate, additives — anthracite, dolomite — and binders are prepared in terms of particle size and chemical
The ratio in the output from the three main pelletizing technologies changes depending on practical circumstances, such as iron ore reserves, iron ore types, market demand, required investment, etc. The ratio for GK pellets has increased to 77.0% in 2018 from 7.0% in 2000, while the ratio for shaft furnace pellets has dropped to 14.9% in 2018 ...
Design and development of improved sintering and pelletizing processes. Lumpy iron ores are extensively used in the production of steel all around the world. ... The objective of iron ore agglomeration is to generate a …
Pelletization involves converting iron ore fines into compact pellets, which are then used in blast furnaces or direct reduction iron processes, contributing to more sustainable and efficient steel …
THE SCARABAEUS® 7500 PELLETIZING DISC THE SCARABAEUS ® 7500 PELLETIZING DISC Sustainable and efficient production of iron ore pellets IMPROVED PRODUCT QUALITY INCREASED PRODUCT OUTPUT REDUCED CO2 EMISSIONS IRON ORE & PELLETIZING TECHNOLOGY IMPROVE RESOURCE EFFICIENCY Iron ore is the main source of iron and …
For Primetals Technologies, this is the first step in pelletizing plant design. Everything starts with iron ore. Primetals Technologies partners with institutions and labs worldwide to test iron ore and provides testing facilities for pellets in Leoben, Austria. However, analysis of the iron ore is essential before delving deeper into pellet tests.
This chapter aims to provide an overview and the evolution of iron ore pelletizing process including: Pelletizing process and raw materials. Balling technologies. Bonding mechanisms. Evolution of binders for iron ore pelletizing. Induration technologies. Challenges …
Iron ore pelletizing is an essential industrial process that transforms powdery iron ore into uniform, robust pellets, serving as a premium feedstock for blast furnaces and direct reduction reactors. ... Advancements in pelletizing technology focus on enhancing the efficiency and sustainability of the process. Innovations in induration ...
Profound knowledge of iron-ore characteristics, including variances in chemistry and regional factors, is key to creating the ideal pelletizing plant for high-quality pellets. Since 2015, Primetals Technologies' innovative …
Figure 3 – Total pelletizing capacity ever built vs. type of ore vs. technology ( 1, 3 ) Pelletizing is the most engineered agglomeration technology.
A brief introduction to recent developments in iron ore pelletizing is provided in this chapter, including the world output of fired pellets, pellet production processes, preparation of pellet ...
A brief introduction to recent developments in iron ore pelletizing is provided in this chapter, including the world output of fired pellets, pellet production processes, preparation of pellet feed, inorganic and organic binders, and new additives. Throughout the chapter, the authors have used a difficult pellet feed, that is, a Brazilian specular hematite concentrate, as an …
Referred to as Circular Pelletizing Technology (CPT), this iron ore agglomeration facility is characterized by its highly compact layout and light-weight construction design. This is the basis for efficient and cost-effective installation at a mining site or within an iron and steel complex. Pellet production capacities range from 800 000 t/a ...
Our iron ore pelletizing systems combine the best features of both technologies to provide the most modern plant and to produce pellets at the lowest cost and highest quality. Pellet plants sized from 1.2MTPA to 9MTPA; Engineering and design of complete plants from ore receiving to pellet discharge;
In the last years, pelletizing has been playing an important role in iron ore mining and in iron production (iron making and direct reduction). Some factors have contributed to this fact as …
Iron ore pelletizing is an essential industrial process that transforms powdery iron ore into uniform, robust pellets, serving as a premium feedstock for blast furnaces and direct reduction reactors.
The binder is an important additive widely applied in pelletizing iron ore concentrates, making iron ore pellets available as feedstocks for blast furnace ironmaking or direct reduction processes ...
North American 4235 EcoFornax™ LE ultra-low NOx pelletizing burner . Iron pellet producers around the world are continuing to pursue cleaner and more efficient production processes.The expectation is that all pellet producers will adopt combustion technologies that will significantly improve energy consumption, lower furnace emissions and sustain operational flexibility.
Pelletizing of iron ore concentrates in pelletizing discs leads to narrow grain size distributed pellets with smooth surface. Pelletizing – how? The process chamber of a pelletizing disc is made by an inclined, rotating, flat cylindrical pan.
05/19/2021 - Primetals Technologies has signed a licensing agreement allowing it to sell and supply Outotec Oyj's straight grate iron ore pelletizing technology in the Indian market. In a statement, Primetals Technologies said the license gives it the exclusive right to execute pelletizing plants in India based on straight grate ...
• There are several iron ore pelletizing processes/technologies available in the world. However, currently, Straight Travelling Grate Process and Grate Kiln Process are more popular processes. • The pellet plant in eastern region use either travelling grate technology with dry grinding or Grate Kiln technology with wet grinding technology.
Pelletizing, or balling, carried out through either a disc pelletizer or rotary drum, is a key part of efficiently and sustainably producing steel from iron ore fines of varying sources. FEECO is a leader in feasibility testing, custom disc …
Customer Pro Minerals Pvt. Ltd., India. Type of plant Circular Pelletizing Plant (191 m²), output 1.0 mtpy. Our solution Our solution for the production of merchant pellets was devised as a green-field installation of a Circular Pelletizing Plant (CPT), including several associated facilities such as units for grinding and filtration and a beneficiation plant for upgradation of low-grade iron ...
A brief introduction to recent developments in iron ore pelletizing is provided in this chapter, including the world output of fired pellets, pellet production processes, preparation of...
Get uniform pellets with excellent metallurgical and physical properties. 's traveling grate pelletizing plant is the industry's leading induration technology for iron ore pellet production for a wide range of plant capacities.
حقوق النشر © 2024.Artom كل الحقوق محفوظة.خريطة الموقع