Multi-material crushing pressure model.
A cone crusher is a machine that crushes rock materials with high efficiency and low power consumption; it is one of the typical road construction equipment.
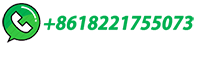
A cone crusher is a machine that crushes rock materials with high efficiency and low power consumption; it is one of the typical road construction equipment.
The operational part of the cone crusher is the crushing chamber, which consists of a mantle and a concave liner. As shown in Fig. 1, the axis of the mantle intersects the axis of the crushing chamber at point O, which is the pivot point.The angle between the two axes is γ, which is the eccentric angle.During operation of the crusher, the mantle moves around the axis of the …
This model predicts the particle shape over the entire gradation produced by a crusher. This allows for the particle shape of the final product to be predicted. The model depends on the feed gradation and crusher setting. The optimization routine will, therefore, be able to find the best machine parameter settings for the plant.
There are a sufficient number of works devoted to modeling crushing machines. Nevertheless, the fact that there are a large number of working conditions, and the ongoing development of science and technology, require continuous improvement and specification of the models intended for crushing processes and those of the devices concerned. However, there …
Ensuring excellent stone crusher performance and uptime over time Stone crushers need engines with a correctly specified torque curve and an ability to handle both heavy and light loads effortlessly. The engine needs to run at a high capacity, and do so steadily without losing speed when handling heavy stones and rocks, or high volumes of sand ...
Based on 's crushing technology, the MKIII is a high-speed primary gyratory crusher to deliver up to 30 % higher capacity and 70 % lower downtime in a comminution circuit. With a 1780 mm feed, the Superior MKIII 7089 has one of the largest feed openings on the market. Designed for the most demanding primary crushing conditions and with the ...
This article provides a comparative analysis of blow bar used in different crusher applications, focusing on the materials, design, wear resistance, and application suitability. Materials Used in Blow Bar. Blow bar is manufactured from various materials, each offering distinct advantages and drawbacks. The choice of material affects the blow ...
Good component efficiency and part performance pre-evaluation is essential to a solid design. The aggregate production requires the consideration of several crushers, feeders and screens. This is not intended to be a typical …
In Hydrocone crushers, the closed-side setting (CSS), which controls the size of the crusher's discharge product, is limited by and adjusted through pressure. This sets special demands on the wear parts. The liners that Mexicana de Cobre was previously using could not fulfill the performance requirements until the end of their wear life. The ...
Crushing Plant Optimization zTechnical and economical zDesign and operation zBestpossibleperformanceforagivenmarketsituationBest possible performance for a given ...
The gyratory crusher is essential in the primary crushing process of the ore (Pothina et al., 2007); the productivity of the entire ore processing can be improved by increasing the yield and quality of the product (Cleary et al., 2020). For extrusion crushers, the grinding of ore particles is based on the progressively narrowing space between ...
Feed gradation, crusher setting and crusher speed affect the energy consumption during rock crushing (Fladvad and Onnela, 2020). From a practical point of view, the question how energy consumption changes with reduction of aperture size on the jaw crusher in order to produce finer aggregates, while keeping all other crusher setings the same is ...
Our Chamber Optimization experts help you to identify bottlenecks and optimize crushing performance from a single crusher to the full circuit. has designed and manufactured crushers for decades.
To optimize the crushing chamber of the gyratory crusher, the discrete element method (DEM) is used to explore the influence of the concave curve height, concave curve radius, eccentric angle, and ...
A dynamic model of the working mechanism of a compound pendulum jaw crusher with clearance is established by the Lagrange multiplier method (LMD) based on the L-N contact force model and modified Coulomb friction force model. The correctness of the dynamic model is verified by MATLAB and Adams comparison simulation, and the best selection range of driving …
The fixed cone mass and moving cone mass of a balancing crusher are decreased by 78.9% and 22.8%, respectively, compared to without the balancing mechanism. Simulation parameters for MBD-DEM.
jaw crusher, because it affect the performance of crusher. If the stroke value become smaller, the wear of crusher liner reduce a lot, the life of liner become longer, the product granularity become more stable and the consumption of energy decrease greatly. So the stroke value is chosen as the objective function, that is y x S S
There are a number of variables that can affect crushing capacity, including liner choices, consistent or inconsistent feed, crusher speed, closed …
Evaluating and optimizing the performance of a crusher plant is essential for maximizing productivity, efficiency, and profitability. By assessing key performance indicators …
Larger 7-foot bowl diameter and optimized crusher geometry enable higher throughput compared to smaller crushers. Enhanced material flow characteristics minimize blockages and maximize crusher availability. Improved Product Quality: Precise cone setting adjustment ensures consistent product size and shape.
Inertia cone crushers are widely used in complex ore mineral processing. The two mass variables (fixed cone mass and moving cone mass) affect the dynamic performance of the inertia cone crusher. Particularly the operative crushing force of the moving cone and the amplitude of the fixed cone are affected, and thus the energy consumption of the crusher. In …
Introducing the new ACS-c 5 for 800i cone crusher series – our most powerful user-friendly automation system to date. By integrating the powerful capabilities of all crusher modules and subsystems into a single automation system, we've made 800i crushers easy and intuitive to …
Minerals 2021, 11, 163 3 of 18 eccentric vibrator (B3); O4 is a planar joint between B3 and B4; O5 is a ball-pin joint between B3 and the connecting shaft (B5); O6 is a universal joint between B5 and the drive shaft (B6); O7 is a revolute joint between B6 and the ground (B0). Figure 1. Schematics of the inertia cone crusher: (a) vertical cross-section and (b) simplified multi-body …
• In a cone crusher the stones are crushed with both SPB and IPB as the material moves down through the chamber. • The relative amounts of IPB and SPB depends on factors like chamber design, crusher geometry, speed, css, eccentric throw, and others. SPB . IPB . Fines . Less : More . Shape : Flaky . Cubic : Force .
1. Introduction. Crushers are widely used in the mining, mineral, road construction, and other industrial sectors to crush a variety of raw materials [1 – 3].According to the different structural types, the commonly used crushers can be divided into the jaw crusher, gyratory crusher, and cone crusher [].Due to decades of theoretical research, they have evolved from …
According to Eloranta (1995) and Evertsson (2000), the crushing process in a cone crusher can be described by dividing the crushing chamber into a number of different crushing zones (see Fig. 2); each corresponding to a crushing event performed by a compression.The crushing process in a cone crusher can thus be modeled as a series of consecutive …
The crushing chamber is the core component of a cone crusher, consisting of mantle and concave parts. Reducing the impact of crushing chamber wear on the performance of cone crushers and the ...
The main objective is to investigate the impact of various crushing parameters like feed rate to jaw crusher and eccentric speed of Jaw crusher, closed side setting and throw in cone crusher. For optimization, Taguchi Design of Experiment (DOE) have been perform by considering eccentric speed, feed rate, closed side setting & throw as the ...
Crusher Yield Income Optimization of a Final Crushing Stage • What difference does it make? • Running the crusher 0.08'' off: – Decrease the profit by 58.5 $/h – Running the crusher at 1600 hours per year: 58.5*1600=$93600 Planning Sampling Analysis Optimization 0 500 1000 1500 2000 2500 0.60 0.65 0.70 0.75 0.80 0.85 0.90 0.95 1.00 ...
Jaw crusher machines are used in the mining and construction industry for crushing rocks and mineral ores to the appropriate sizes for direct application or further processing. During the crushing ...
حقوق النشر © 2024.Artom كل الحقوق محفوظة.خريطة الموقع