Process characteristics of clinker and cement production
• ETHZ has simulated and adapted the CAP system to different cement-plant flue gases; • New rate-based model was developed and used to validate full-scale CAP simulations for cement …
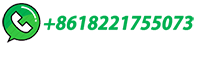
• ETHZ has simulated and adapted the CAP system to different cement-plant flue gases; • New rate-based model was developed and used to validate full-scale CAP simulations for cement …
The cement manufacturing process is a complex one involving several steps. Each step in the process plays an important role in the overall quality of the finished product. ... 1510°C (2750°F): Cement clinker is formed; The kiln is angled by 3 degrees to the horizontal to allow the material to pass through it, over a period of 20 to 30 minutes ...
Cement manufacturing equipment needs to withstand the heat and the abrasive material from which cement is made. Making cement involves combining raw materials including limestone, clay, and shale, which are milled into a very fine powder after being mined. These materials are then mixed with other ingredients according to their end-use. This mixture is then fired in a kiln …
The cement manufacturing process is a sector that constantly changes and develops, and it is a very wide and complex sum of processes. In fact the cement industry is striving to be competitive and sustainable so as to generate the high-quality and efficient construction materials that our society needs [].Actually, the objective is to be able to …
This study uses machine learning methods to model different stages of the calcination process in cement, with the goal of improving knowledge of the generation of CO2 during cement manufacturing. Calcination is necessary to determine the clinker quality, energy needs, and CO2 emissions in a cement-producing facility. Due to the intricacy of the …
So the calcination of cement clinker is the key process of cement production. Among them, clinker kiln as the clinker production equipment is the core of the whole cement production line. Both its quality and manufacturing technology have a direct impact on cement products, so the choice of clinker kiln is very important for cement manufacturers.
If you want to work in cement production, there are five crucial cement manufacturing machines you need to know, they are cement rotary kiln, shaft kiln, cement vertical mill, cement ball mill, and cement roller press. Cement Rotary …
Explore the significance of clinker grinding in cement manufacturing, from particle size reduction to improved reactivity and quality control. Learn how this integral process transforms clinker into the final …
Cement manufacturing mainly includes five steps: raw material preparation, raw material calcination, clinker grinding, cement packaging, and transportation. Besides, we may need some other production lines to cooperate with the production of cement, such as the stone crushing plant, cement grinding unit, and fly ash processing plant .
AGICO Cement provides cement equipment of clinker production, including rotary kiln, preheater, and precalciner, start cement plant now! Skip to content +86 . info@cement-plants. about. blog. ... Find out single …
Global cement production has reached 3.9 billion tons. However, the clinkerization process, which is the basis of cement production, is responsible for an approximate annual global CO2 emission of 2 billion tons. As part of CEMBUREAU's 5C strategy, the European cement industry aims to achieve carbon neutrality throughout the cement-concrete value chain by 2050. This article is …
The clinker cooler, also known as grate cooler or cement cooler, it is a necessary equipment of cement clinker production.The clinker cooler is mainly used to cool and transport the cement clinker. At the same time, cement cooler also provide hot-air for rotary kiln and calciner, it is the main equipment of heat recovery for burning system.. The cooler will make a sufficient heat …
It can not only grind cement clinker but also process cement admixture, such as gypsum, fly ash, furnace slag, coal gangue, etc., realizing a stable, high-quality and automated cement production. Unlike the cement production line, the …
Clinker cooling is one of the important processes in cement production. Improving the cooling effect is not only beneficial to improve the quality and grindability of clinker, reduce the power consumption of the cement mill, but also can reduce the clinker temperature, recover the waste heat, and create favorable conditions for subsequent cement handling, storage, or transportation.
The cement manufacturing process mainly includes four steps: resource extraction, raw material preparation, clinker calcination, cement grinding 17,18, and fossil fuel burning 19.
The main part of the manufacturing process of clinker takes place in the kiln. The stages in the kiln phase are as follows: Evaporation of free water: A pressure above atmospheric is required …
A: Cement is the final product obtained by grinding clinker with added gypsum, while clinker is a raw material in the cement production process. Q: Why is clinker so crucial for construction? A: Clinker provides the essential binding properties in cement, ensuring the strength and durability of concrete structures.
After cooling, the clinker can be stored in the clinker dome, silos, bins, or outside in storage piles. The material handling equipment used to transport clinker from the clinker coolers to storage and then to the finish mill is similar to that used to transport raw materials (e.g. belt conveyors, deep bucket conveyors, and bucket elevators).
AGICO Cement provides cement equipment of clinker production, including rotary kiln, preheater, and precalciner, start cement plant now!
In this work, we employ machine learning methods to perform effective quality control for cement production through monitoring and predicting the density of free calcium oxide (f-CaO) in cement ...
Raw Grinding: Initially, a ball mill with a high-efficiency separator is utilized to ensure uniform particle size in the raw mix, essential for the subsequent stages of the manufacturing process. Clinker Grinding: The main process in cement …
The cement rotary kiln is the core equipment in wet and dry cement plants for producing clinker in cement. It is designed for harsh environments, with a long lifespan, using a burner at the kiln …
This is followed by the last stage of cement manufacturing, in which the clinker is ground with gypsum to prolong the setting time of cement through (6) single mills with a length of (16) m and a diameter of (6) m, and weighing up to (180) tons and at a grinding rate of (350) tons / hour per mill with a total grinding rate of (2100) tons / hour.
Excess free lime, for example, results in undesirable effects such as volume expansion, increased setting time or reduced strength. Several laboratory and online systems can be employed to ensure process control in each step of the cement manufacturing process, including clinker formation. How cement manufacturers can help ensure cement quality
Low-carbon fuels, feedstocks, and energy sources can play a vital role in the decarbonization of clinker production in cement manufacturing. Fuel switching with renewable natural gas, green hydrogen, and biomass can provide a low-carbon energy source for the high-temperature process heat during the pyroprocessing steps of clinker production. However, up …
Modern cement plants strive to achieve maximum thermodynamic efficiency during the manufacturing of cement clinker [8]. To further improve the sustainability of cement production, optimization of the clinkering process is a key factor. ... A machine learning approach for clinker quality prediction and nonlinear model predictive control design ...
A cement plant of our industry partner is used in this study. As shown in Figure 1, the cement kiln takes the raw kiln feed and thermally transforms this into cement clinker.This process uses multiple heat exchangers represented by four main production zones: a 5-stage Single-String Preheater Tower, a PyroClon Calciner (Precalciner) and Tertiary Air, a KHD Pyro …
The clinker manufacturing process The preheating of the material takes place in pre-heater cyclones fitted with a pre-calciner fired with petroleum, natural gas or coal. The calcinations of the material begin during this stage, changing its phase to the oxide phase for each component to be ready for the burning process.
While each cement plant may differ in layout, equipment, and appearance, the general process of manufacturing portland cement is the same: crushed limestone and sand are mixed with ground clay, shale, iron ore, fly ash and alternative raw materials. ... The clinker comes out of the kiln red-hot with a consistency like a lava flow. It is quickly ...
Raw Materials Crushing, Storing and Grinding. Clinker calcination is the most crucial part of the whole process of cement manufacturing. At this stage, ground raw materials will be sent into the cement kiln and be heated at a high …
حقوق النشر © 2024.Artom كل الحقوق محفوظة.خريطة الموقع