Optimization of the Clinker Production Phase in a Cement Plant …
Subsequently, clinker is grinded and combined with other components, such as calcium sulfate or pozzuolan, obtaining the desired type of cement. The clinker production phase at issue processes about 899000 tons per year of raw meal, using 59100 tons per year of fuel (coal); about 584000 tons per year of clinker are produced.
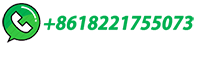