How Iron Is Made
How Is Iron Made? To convert iron ore into metallic iron, oxygen and impurities must be removed. This process requires heat and a reducing agent, a substance that combines with the oxygen and releases it from the ore.
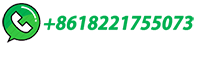
How Is Iron Made? To convert iron ore into metallic iron, oxygen and impurities must be removed. This process requires heat and a reducing agent, a substance that combines with the oxygen and releases it from the ore.
This process generates iron ore filter cake which needs to be pelletized so that it can be used in an iron making process. ... The large grate machines are 4 m wide and are capable of producing more than 3 million tons of pellets per year. Circular grate machines have also been designed and are in operation.
Introduction. Iron is the backbone of the world we have built around us and it is the basic ingredient of steel (iron plus carbon). Iron is a very useful metal because it can be mixed with other metals to make a whole variety of 'alloys' which are even stronger and don't rust easily and can be shaped into products from cars to pins, appliances to buildings, bridges …
Iron making evolved over a few thousand years. Using the ancient "bloomery" method, iron ore was converted directly into wrought iron by heating the ore while at the same time melting the ore's impurities and squeezing them out with hand hammers. This is also called the "direct process." By the 1100s water-powered hammers replaced hand hammers ...
Loss on ignition (LOI) in the mineral represents the chemically bonded water which can be removed at high temperatures only. High LOI in iron ore fines has an adverse affect during pellet induration process. High-LOI iron ore fines are required for detailed laboratory pelletization studies and are used in pellet making. The received iron ore is martite–goethitic and …
When iron ore is extracted from a mine, it must undergo several processing stages. Six steps to process iron ore. 1. Screening We recommend that you begin by screening the iron ore to separate fine particles below the crusher's CSS …
Making Iron Directly From Concentrate by Gaseous Reduction H. Y. Sohn1 Received: 25 March 2023 / Accepted: 25 April 2023 / Published online: 12 May 2023 ... reactor · Pilot plant · Burner · Flash Reactor · Human machine interface (HMI) · Computational uid dynamics (CFD) · Reactor design 1 Introduction
Iron, one of the most fundamental elements on Earth, has played a pivotal role in shaping human civilization. The journey of ironmaking techniques spans millennia, evolving from ancient methods rooted in fire and craftsmanship to …
DR process, DRI, HBI, Iron making. Metallization, reformed natural gas, residual elements, Rotary kiln, Direct Reduced Iron and its Production Processes. Direct reduced iron (DRI) is the product which is produced by the direct reduction of iron ore or other iron bearing materials in the solid state by using non-coking coal or natural gas.
Fig 4 Circular sintering machine. Straight line machines are normally used for high capacity sinter plants. The sintering areas of such machines are generally 50 sqm and above. Present straight line machines are installed having widths ranging from 2 m to 5 m and with effective sintering areas ranging from 200 sqm to 600 sqm.
Automation, digitalization and use of the latest technology in everything from bulk materials handling stockyard machines to crushers, screens and samplers give you the highest throughput with less manpower. Our offerings. ... In the iron ore industry, you want the largest possible throughput of iron ore through your processing equipment. ...
Sintering is a thermal agglomeration process that is applied to a mixture of iron ore fines, recycled ironmaking products, fluxes, slag-forming agents and solid fuel (coke).
Iron ore is essential to meeting the demands of the steel industry that continues to build the world around us. Pelletizing, or balling, carried out through either a disc pelletizer or rotary drum, is a key part of efficiently and sustainably producing steel from iron ore fines of varying sources.
The iron ore production has significantly expanded in recent years, owing to increasing steel demands in developing countries. However, the content of iron in ore deposits has deteriorated and low-grade iron ore has been …
You've probably heard of iron ore, but how do we turn a slab of rock into a set of stainless steel surgical instruments or a locomotive? In this article, you'll learn all about iron and steel. A skilled blacksmith can work heated iron …
The iron and steel making processes are the major carbon emissions source in the iron and steel industry. According to China's example of 2004, the iron making process is the most energy-consuming process among all steel industry processes, accounting for 70% of the total energy use of the iron and steel sector [75]. Because of the complexity ...
The pellet making method was studied for production of iron ore pellets with a carbon core. The pellets are to be fired in a sintering machine to produce sintered ores containing carbonaceous ...
Iron ore and iron ore pellets are important sources of iron for manufacturing steel. The iron ore. production has significantly expanded in recent years, owing to increasing steel demands in.
Iron ore pellets are spheres of typically 8-16 mm to be used as feedstock for blast furnaces. They contain 64-72% iron and additional materials, which can adjust the chemical composition and metallurgical properties of the pellets. The iron ore pelletization is the process of converting iron fines less than 200 mesh (0.074 mm) into 8-16 mm pellets.
Iron ore is an ore that can be obtained through mining iron rocks, requiring level 10 Mining, in various places around RuneScape.. Iron is required to craft iron and steel bars, and is also a tertiary ingredient for creating granite crab …
What is sponge iron Sponge iron, also known as DRI (direct reduced iron or direct reduction iron), bulk density 1.6-1.9g/cm3, apparent density 3.4-3.6g/cm3, typical size 4-20mm, is a kind of material produced by the reduction of iron ore with reducing gases such as H2 or CO gas generated from various carbon or hydrocarbon resources. The name is got because iron …
Iron ore, a naturally occurring mineral composed primarily of iron oxides, is mined and processed to extract iron for various industrial applications. This article provides a comprehensive overview of the iron ore processing …
The various advantages of iron ore pellets are given below. Iron ore pellet is a kind of agglomerated fines which has better tumbling index when compared with the iron ore and it can be used as a substitute for the iron ore lumps both in the BF and for DRI production. Pellets have good reducibility since they have high porosity (25 % to 30 %).
What is sponge iron. Sponge iron, also name as direct reduced iron (DRI), is the resulting product (with a metallization degree greater than 82 percent) of solid state reduction of iron ores or agglomerates (generally of high grade), the principal constituents of which are Metallic iron, residual iron oxides carbon' and impurities such as phosphorus, sulphur and gangue …
As societies progressed, humans began to extract iron from terrestrial sources, marking the transition from the use of meteoric iron to smelting iron ore. One of the earliest known methods of iron smelting was the bloomery process. This …
Iron making - Download as a PDF or view online for free. ... deep drawing parts, chain, pipe, wire, nails, some machine parts. Medium carbon steels (C =0.25% to 0.55%) Properties: good toughness and ductility, relatively good strength, may be hardened by quenching Applications: rolls, axles, screws, cylinders, crankshafts, heat treated machine ...
The present work provides information on the iron ores that form part of the mineral mix which, once granulated, is loaded onto the sinter strand where it is partially melted at a temperature of ...
The main iron ore mining equipment includes jaw crushers, ball mills, magnetic separators, spiral classifiers, jig concentrators and related auxiliary equipment such as ore dryers. Jaw crusher reduces the hard iron ore into a smaller size, it has a high iron crushing ratio, feeding and crushing capacity, uniform texture, good grain shape.
Beneficiation of Iron Ore and the treatment of magnetic iron taconites, stage grinding and wet magnetic separation is standard practice.This also applies to iron ores of the non-magnetic type which after a reducing roast are amenable to magnetic separation. All such plants are large tonnage operations treating up to 50,000 tons per day and ultimately requiring …
Usually, Iron Ore is manufactured and converted into Pellets. These are oval lumps of iron ore that are hardened using fuel. This process of converting iron ore into pellets is known as Pelletization. Iron Ore Pellets are then used in the production of steel. Pellets are usually preferred instead of raw Iron Ore because it allows for maximum ...
حقوق النشر © 2024.Artom كل الحقوق محفوظة.خريطة الموقع