Porosity in different region of heat-treated pellet versus CCS …
from publication: Phase and Microstructural Characterization of Iron Ore Pellet and Their Relation with Cold Crushing Strength Test | The use of microstructural characteristics as a quality ...
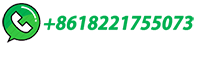