Crushers Selection Guide: Types, Features, Applications
There are several types of industrial crushers available to industrial buyers. These types include: Cone or gyratory crushers insert feed via a cone-shape bowl and crush it with a spinning or gyrating head. HPGR (high pressure grinding rollers), roll/roller crushers, or mineral sizers use two large rollers or a roller and a flat surface. The ...
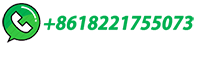