Characterization and comparison of deposits in a coal-fired …
Compared to iron ore acidic pellet production, the deposit problem in kiln became more severe to produce iron ore fluxed pellets. This study characterized the deposit samples in a grate-kiln process for iron ore fluxed pellet production. The deposited samples were analyzed by chemical analysis, XRD, SEM-EDS, and thermodynamic software.The deposits contained …
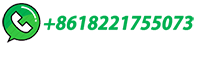