Mass balance of the kiln system [43].
Rotary kilns are industrial furnaces used for the continuous processing of raw materials at high temperature, consisting in long steel cylinders lined with refractory bricks and revolved by...
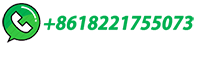
Rotary kilns are industrial furnaces used for the continuous processing of raw materials at high temperature, consisting in long steel cylinders lined with refractory bricks and revolved by...
The rotary kiln is a counter current heat exchanger with a very complicated direct heat transfer process taking place between the hot gas, the kiln wall and the moving solid bed (Fig. 10.5). The thermal energy requirement ranges from about 4100 kJ/kg to as much as 6000 kJ/kg or more for small rotary kilns producing floury or highly calcined ...
the kiln energy balances analyzed. This is affected by APDL programming, integrating it within the ... The mass flow speed of the material along a rotary kiln is not constant. However, in an ...
Similar material balance equations are written for. ... This paper deals in particular with the development of a dynamic model which describes the behavior of a rotary kiln (primary combustion ...
As a rule, a material balance () is established for the process of calcining petroleum coke, so that both raw material consumption and Calciner's equipment condition can be assessed. So, the paper describes the activities that are aimed at measuring petcoke losses (actual losses) during calcination in a rotary kiln.
He also developed material balance equations for determining the rate of species formation within the material bed, and qualitatively was able to represent the behavior of actual rotary kilns. Barr et al. [7] performed a study using a pilot-scale rotary kiln and compared it to the results of a mathematical model. A large increase in net heat ...
Rotary Kilns Transport Phenomena and Transport Processes ... 9 Mass and Energy Balance 239 9.1 Chemical Thermodynamics 239 9.2 Gibbs Free Energy and Entropy 240 9.3 Global Heat and Material Balance 243 9.4 Thermal Module for Chemically Reactive System 244 …
The set of equations must represent real heat evolutions or absorptions in the process as much as possible Example - Limestone of 84% CaCO3, 8% MgCO3, 8% H2O is calcined in a rotary …
Table 3 shows the mass balance of the rotary kiln, in other words, amount of raw materials entering and leaving to and from the unit. The calculated energy flows of the rotary kiln are given...
Most rotary kilns are direct fired – with a flame shooting into the kiln from the discharge end (the fire wall). As the kiln rotates, the heated material climbs the kiln wall before flopping down and flipping over. With each flop, the material travels a short distance along the length of the kiln because it is at a slight angle.
In recent times, investments in rotary kilns using the rotary kiln and electric furnace (RK-EF) method for producing nickel, a primary material for secondary batteries, have been actively progressing in nations like Indonesia . In the RK-EF process, a rotary kiln serves as a preliminary reduction process to create calcine, which is sintered ...
Functionality of Rotary Kilns. Rotary kilns serve a significant role in processing raw materials into final products. Here's how they function: Rotation: The shell's rotation enables the material to tumble and mix, promoting even heating. Temperature Control: Temperatures in the rotary kiln can reach extraordinarily high levels, necessary for initiating chemical reactions or phase …
Reaching the outlet of the rotary kiln, the material is discharged into the cooler where lime is cooled and the secondary air is preheated. ... Exhaust gases have the major portion of heat loss in this process (near 70%). True balance of energy is another evidence for validity of the model. Download: Download high-res image (65KB) Download ...
Nielsen studies the devolatilization and combustion of tires, and pinewood in a pilot-scale rotary kiln, under conditions similar to those of the input end of the flour. first) to rotary kilns. The main trends regarding alternative fuel utilization in the material inlet end of cement rotary kilns found by Nielsen are as follows:
The rotary kiln is used in many solid processes, including drying, incineration, heating, cooling, humidification, ... design offered a modification of previous kilns: material and fuel were fed into the kiln from above. The baked clinker flowed out of the bottom. The great revolution in the continuity of the cement production process
How to calculate the dimension of the rotary dryer for wood chips? The information as follows: The material: wet wood chips, sawdust. The output: 3ton per hour. A:Drying intensity (35kg/m 3 h) G 1 :Dry Material Production (3t/h) V:Dry Space needed(m 3) W 1 :Initial Moisture Content(55%) W 2 :Final Moisture Content(12%) Material ...
This study develops a comprehensive cradle-to-gate (raw material to iron product) life cycle assessment of three distinct technological pathways for producing DRI: direct coal reduction in a rotary kiln (rotary kiln DRI process), coal gasifier and shaft furnace (coal gasifier DRI process), and reformed natural gas and shaft furnace (NG reformer ...
The rotary kiln is slightly inclined at an angle 2.5 degree and rotated by AC variable speed motor at a variable speed ranging from 0.2 rpm (revolutions per minute) to 1.0 rpm. Due to inclination and rotary motion of the kiln, the material travels from feed end to the discharge end of the kiln in around 7 hours to 8 hours.
Rotary Kiln *Venkataramana Runkana 1,, Pradeep Kumar Vasant Natekar 1, Viswanadh Bandla and Gyanaranjan Pothal 2 ... gas and the solid phases, material balances for individual
The rotary kiln is a slightly inclined steel cylinder that rests on supports (bearing rollers) with an interior lining; it is equipped with a rotating motor that induces a turning motion. …
Bahan Imbuh Fluks Adatif Batu Kapur rotary kiln serta Kebutuhan Material Balance Proses Reduksi Rotary Kiln. Proses Reduksi Bijih Besi Di Rotary Kiln dengan kapur bakar rotary kiln atau burnt lime rotary kiln atau gas reduktor CO di rotary kiln dan pembakar parsial di rotary kiln.
representing the material balances, heat balances and chemical reactions along the kiln [7, 13, 11, 2, 10]. In a previous publication [4], the rotary coke calcining kiln processes were simulated using a commercial simulator. The reactions were simulated as conversion reactions and the values of the conversions were obtained from real kiln data.
Mass Balance of a Kiln System. The following diagram illustrates an example of the mass flows in a cement plant and the mass balance of a kiln system from raw meal (RM) to clinker. Figure 2: Schematic diagram of material and dust flows …
In this paper, we report on stages 2 and 3 mentioned above, clarifying the material balance with energy consumption in an externally heated rotary kiln on a bench scale and the scale-up simulation of the energy and economic balances of a 200-kg/h plant.
Based on the principle of mass balance and material balance, according to GB/T2589-2008, the energy audit guidelines and the general rules for the calculation of comprehensive energy consumption were followed, according to the field tracking survey of the energy consumption data of aluminate cement produced by the cement clinker production base ...
For evaporating moisture from concentrates or other products from plant operations, Rotary Dryers are designed and constructed for high efficiency and economy in fuel consumption. Whenever possible to apply heat direct to the material to be dried, Rotary Dryers of the Direct Heating Design are used. If it is not possible to apply heat direct to the material to be dried, …
Get instant access. Purchase Access. Read this article for 48 hours. Check out below using your ACS ID or as a guest.
Liu et al. [19] developed mass and energy balances to assess the dryer, rotary kiln, and electric arc furnaces. The rotary kiln furnace showed potential for waste heat recovery from the discharged ...
Download scientific diagram | Heat balance of cement kiln [5]. from publication: Using the adsorption chillers for utilisation of waste heat from rotary kilns | Waste heat utilisation and its ...
2.4 Material Balance 12 2.5 Energy Balance 15 2.6 Energy Performance Assessment of Key Equipment 15 3.0 Energy-efficient Technologies in Direct Reduction of Iron Process 17 3.1 Waste Heat Recovery for Power Generation 18 3.2 Iron Ore Preheating Rotary Kiln Using Waste Heat Recovery System 20
حقوق النشر © 2024.Artom كل الحقوق محفوظة.خريطة الموقع