SPONGE IRON PRODUCTION FROM ORE -COAL …
In the year 1908 use of tunnel kiln started for iron oxide reduction. This process was invented by E.Sieurin as Hoganas process [3]. In 1954, more kilns came in operation in SWEDEN and …
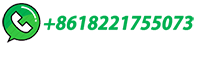
In the year 1908 use of tunnel kiln started for iron oxide reduction. This process was invented by E.Sieurin as Hoganas process [3]. In 1954, more kilns came in operation in SWEDEN and …
The sponge iron process is a process for producing sponge iron, which is porous iron [1]. The raw material used for producing sponge iron is magnetite ore concentrate (Fe 3 O 4 ... they will be placed on a cart and enter a tunnel kiln [1]. The cart will travel through three zones in the tunnel kiln; the pre-heating zone followed by a firing zone
DRI, also known as sponge iron, is the product of reducing iron oxide in the form of iron ore and steel plant wastes into metallic iron, below the melting point of iron and typically in the range of 800–1200 °C. Iron oxide is charged into shaft furnace, rotary kiln, or fluidized beds in the form of pellet, iron ore lumps, or fines. The reduction takes place using gaseous reductants (CO + H ...
These plants use iron ore pellets in the rotary kiln. Raw material mix consisting of iron ore, dolomite and non-coking coal is fed at the one end of the rotary kiln and is heated by coal burners to produce DRI. The product DRI …
Sponge iron production by tunnel kiln method was developed from 1911 as Höganäs method in Sweden. After many modifications, now this process is a sufficient and effective method for sponge iron production. The main …
The process of Tunnel Kiln uses fines of Iron ore and fines of Coal to make DRI of 90% plus metallization. About Sponge Iron/DRI. Sponge Iron, also known as Direct Reduced Iron is the product produced out of using iron ore. The iron ore is processed through reduction process by the use of gas that emits from natural coal gas resource.
The tunnel kiln for firing sponge iron is a low-temperature kiln with a temperature range of 1000~1350℃. The heat source is clean energy natural gas, and the sponge iron reduction tank is transported by a kiln car for production reduction through a tunnel kiln.
Today India stands as the largest producer of coal based sponge iron through rotary kiln process using calibrated ore and non coking coal. However, Rotary kiln process suffers from serious limitations like low productivity and pollution. In this respect fixed bed Tunnel kiln furnace are evolving as an alternative to Rotary kiln process. Iron ore fines and the low grade beneficiated …
Continuous experiment was performed on a industrial scale for the production of sponge iron by using tunnel kiln furnace. Crushed ores were classified into fwo parts of which …
The demo involved crushing iron ore, mixing it with coal to form briquettes, and firing the briquettes in a mini shaft kiln simulating a tunnel kiln. Over five trials with different iron ore sources, the demo successfully produced sponge iron in yields ranging from 2.5% to 63% of the input iron ore weight. CV Asri Keramik promotes tunnel kilns ...
After retention time of 8–10 h in the kiln, the sponge iron is discharged via a transfer chute into a cooler. ... The rotary hearth furnace (RHF) consists of a flat, refractory hearth rotating inside a high-temperature, circular tunnel kiln. The feed to the RHF consists of composite pellets made from a mixture of iron-bearing oxides and a ...
In order to explore the efficacy of iron ore–coal composite pellets over ordinary green pellets, indurated pellets, briquettes as well as standard charging of material in the form of concentric layers of iron ore and coal fines, or their mixture, these pellets were tested at 1,150 °C in a 7 tons per day (7 tpd) pilot tunnel kiln. Reduction of iron ore coal composite pellets in tunnel ...
Iron ore fines and the low grade beneficiated iron ore cake are directly used for manufacturing of sponge iron in tunnel kilns. The material bed in Tunnel kiln being stationary, it does not require high strength and thermal stability of the raw …
1930-1950s Saggers in Tunnel Kilns- Small Shaft Furnace- Rotary Kilns- Hogganas- Wiberg- Krupp & Lurgi- Coal Based ... This produces highly metalized direct reduced iron using rotary kiln. Here solid, liquid and gaseous fuels are used directly in the kiln. The ACCAR process started in ... Sponge Iron & Ferro Alloys 9 In Midrex process reform ...
pellet by non-cooking coal fines under conditions, simulating a tunnel kiln. The results of this investigation indicate that the green pellets could be successfully handled, without generating …
Sponge iron is produced using non-crushing coal through the iron ore reduction process in a rotary kiln. Regeneration takes place at a predetermined temperature and controlled …
Khattoi and Roy tried to explore the use of iron ore–coal composite pellet in a tunnel kiln. However, their process has not been commercialized so far. After the development of the RHF, ... Roy GG (2015) Reduction efficiency of iron ore-coal composite pellets in tunnel kiln for sponge iron production. Trans Ind Inst Met 68(5):683–692.
Sieurin invents sponge iron method The Höganäs Method is invented by engineer Emil Sieurin. The method means reducing iron ore with the help of coke, lime and clay. ... A new modern sponge iron plant is inaugurated with a tunnel kiln measuring a whopping 265 metres. 1985. A period of strong growth In the mid 80's, the Metallurgy area ...
Sponge iron, also called Direct-reduced iron (DRI) is produced from direct reduction of iron ore by a reducing gas produced from coal. The reducing gas is a mixture of hydrogen and carbon monoxide which acts as reducing agent. Rotary Kiln Process
The utility model relates to a sponge iron production device with a two-flame tunnel kiln, which is characterized in that the rear end of a transitional trolley is connected with a stepping motor, the transitional trolley is connected with a trolley, a preheating system, a reducing system and a cooling system are arranged at the upper end of the trolley from right to left, the preheating ...
The main source of phosphorous in induction furnace is sponge iron and cast iron, the quality of which is directly related to quality of iron ore.
Production of sponge iron by Tunnel Kiln technology was developed in 1911 as Höganäs method. Now very popular, the technology has become an effective method for sponge iron production. With the Tunnel Kiln technology, it is possible to build small plants with low investment costs.
Review of Sponge Iron Making Process ... 1930-1950s Saggers in Tunnel Kilns- Small Shaft Furnace- Rotary Kilns- Hogganas- Wiberg- Krupp & Lurgi- Coal Based ... reducing agent like coke breeze or bituminous coal fines are fed into rotary kiln continuously. The temperature of the rotary kiln is kept in the range of 1230- 1260oC. At this ...
PDF | 1- Reduction of mill scale by Hoganas process in tunnel kiln. 2- Crushing the sponge iron cylinder. 3- Annealing of the obtained powder in a belt... | Find, read and cite all the research ...
Kata Kunci : Pasir besi, Desain, Simulasi, Tunnel Kiln, Sponge Iron Ferruginous sand is one of the natural resources that are scattered across Indonesia. Ferruginous sand is generally in the form of magnetite (Fe3O4) and hematite (Fe2O3) with a high content of impurities such as silica, alumina, and titanium oxide.To increase the value of ...
Unloading of DRI / SPONGE IRON (pellets / sponge iron of 2 to 8 mm. size): After Completion of cooling process, DRI (pellets / sponge iron of 2 to 8 mm. size) are ready to leave the Tunnel Kiln.
Keywords: Tunnel Kiln, Iron ore-coal composite pellets, Sponge iron, Thermal efficiency, Carbon utilization efficiency, Percentage metallic iron . 1. INTRODUCTION The tunnel kilns are mostly used by the ceramic industries for heating refractory and ceramic products [1-2]. In the year 1908 use of tunnel kiln started for iron oxide reduction. This
Hi, you can read this article, please {Production of Sponge Iron through Tunnel Kiln Process}, by Swaren Bedarkar. Cite. Hadi Poorhosseinali. Isfahan University of Technology. Hi.
Performance results of reduction process to produce a finish Sponge Iron with increased Fe content of 51.72% to 78.79% with 36.68% metallization degree (Jogja samples) and from 52.93% to 57.90% ...
Innov Engineering advanced tunnel kiln technology is arguably the most sufficient and effective method for sponge iron production which allows for economically feasible plants.
حقوق النشر © 2024.Artom كل الحقوق محفوظة.خريطة الموقع