The six main steps of iron ore processing
Learn about the steps involved in iron ore processing, from crushing and grinding to separation. Contact Multotec experts for guidance on iron processing.
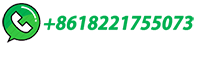
Learn about the steps involved in iron ore processing, from crushing and grinding to separation. Contact Multotec experts for guidance on iron processing.
Iron ore handling, which may account for 20–50% of the total delivered cost of raw materials, covers the processes of transportation, storage, feeding, and washing of the ore en route to or during its various stages of treatment in the mill.. Since the physical state of iron ores in situ may range from friable, or even sandy materials, to monolithic deposits with hardness of …
of oxygen from iron ore in its solid form. The iron used in the steelmaking process is currently chemically reduced from iron ore through the use of fossil resources – natural gas or coal. This process is known as Direct Reduced Ironmaking (DRI). Carbon combines with the oxygen in the iron ore, producing metallic iron and a carbon-rich ...
This kind of iron is called Cast Iron and has a slightly lower carbon content 2 – 3 %. This is even harder than pig iron. Wrought Iron/ Malleable Iron. Wrought iron is the purest form of iron available commercially available and is prepared from cast iron by heating cast iron in a furnace lined with Haematite (Fe 2 O 3). The Haematite reacts ...
The manufacture of iron ore involves the process of reduction. Important ores of iron: Haematite, Magnetite. This Question Belongs to General Knowledge >> Chemistry
Iron ore is converted into various types of iron through several processes. The most common process is the use of a blast furnace to produce pig iron which is about 92-94% iron and 3-5% …
The blast furnace and direct reduction processes have been the major iron production routes for various iron ores (i.e. goethite, hematite, magnetite, maghemite, siderite, etc.) in the past few decades, but the challenges of maintaining the iron and steel-making processes are enormous. The challenges, such as cumbersome production routes, scarcity of …
Direct-Reduced is produced from the direct reduction of iron ore to iron by a reducing gas or elementary carbon produced from natural gas or coal. Many ores are suitable for direct reduction.
The steel making process starts with the melting of iron ore in a blast furnace, where impurities are removed and carbon is added. Secondary steelmaking involves refining the composition by adding or removing elements …
Iron processing - Smelting, Refining, Alloying: The primary objective of iron making is to release iron from chemical combination with oxygen, and, since the blast furnace is much the most efficient process, it receives the most attention …
Today, the manufacturing of steel is done by using one of these two methods: Blast furnace: The blast furnace process, also known as the basic oxygen process (BOP), combines raw iron ore with small amounts of steel scrap metal into a furnace. Then, pure oxygen is blown into the furnace, raising its temperature.
Ferrous metal production and ferrous slags. George C. Wang, in The Utilization of Slag in Civil Infrastructure Construction, 2016 2.4 Steelmaking processes and steel slag formation. As seen in Fig. 2.1, crude iron is refined in a BOF or an EAF to become crude steel.It may also undergo a second refining in a ladle furnace. The BOF steelmaking process is currently the dominant …
Quality requirements of iron ore for iron production. L. Lu, ... D. Zhu, in Iron Ore, 2015 16.4 Summary. The BF ironmaking process is currently the dominant process for providing steelmaking raw materials worldwide. However, the BF process relies heavily on metallurgical coke and involves cokemaking and sintering operations, which often attract serious environmental …
Steel, an alloy primarily composed of iron and carbon, is a crucial material in modern construction and manufacturing due to its strength, flexibility, and durability. The process of making steel involves extracting iron ore, purifying it through beneficiation processes, smelting the purified ore into molten iron which is then further processed to reduce its carbon content …
Direct-Reduced is produced from the direct reduction of iron ore to iron by a reducing gas or elementary carbon produced from natural gas or coal. Many ores are ... The manufacturing of iron from iron ore involves the process of. Oxidation; Reduction; ... -> The selection process for SSC CPO includes a Tier 1, Physical Standard Test (PST ...
Iron ore pelletizing is an essential industrial process that transforms powdery iron ore into uniform, robust pellets, serving as a premium feedstock for blast furnaces and direct reduction reactors. This process has witnessed significant advancements since its inception, primarily driven by the escalating requirements of the steel industry, which demands higher …
To produce steel first the iron ore is heated and melted in a furnace. The impurities are then removed from the molten iron. Carbon and other required alloying elements are added to make steel. ... Thank you for basic process, The normal steel manufacturing procedure is to melt the scrap, which is rebarbarized with coke, anthracite, or broken ...
The manufacture of stainless steel involves a series of processes. First, the steel is melted, To make stainless steel, the raw materials—iron ore, chromium, silicon, nickel, etc.—are melted together in an electric furnace.
Steel manufacturing is a complex process that involves numerous stages, from mining and refining iron ore to creating finished products. Each step requires precision, expertise, and state-of-the-art technology to produce high-quality steel products that meet the demands of a rapidly evolving global economy.
In the latest report of the engineers at Trollhattan, it is stated that the power consumption per ton of pig iron varies in proportion to the iron content of the ore. A poor ore and pig iron high in silicon and manganese require more …
Manufacturing: Iron is involved in the production of various goods, including machinery, tools, and hardware, due to its strength and workability; Production of Iron. The production of iron primarily involves the extraction and processing of iron ore, a process that includes several key steps: Mining: Iron ore is mined from the earth, ...
The process involves three primary raw materials: iron ore, coke (a high-carbon form of coal), and limestone. These materials are charged into the blast furnace, and intense heat generated by burning coke causes a chemical …
The sintering process is an intricate system with a protracted process flow. The steps in the manufacturing line are primarily composed of the ingredients and mixing process, the sintering operation process, and the treatment of the sintered ore [39, 40].2.2 Important parameters and characteristics of sintering process. As shown in Fig. 2, all variables affecting …
Direct reduction iron making: This method involves the reduction of iron ore into metallic iron without melting it. The process involves the use of a reducing gas that reacts with the iron oxide in the iron ore to produce iron. This method is often used …
The process of mining iron ore involves extracting the ore from the earth's crust using heavy machinery and explosives. The extracted ore is then crushed and screened to remove impurities before being transported to a processing plant.
The production of iron from its ore involves an oxidation reduction reaction carried out in a blast furnace. Iron ore is usually a mixture of iron and vast quantities of impurities such …
Zinc processing - Ores, Refining, Alloying: Zinc ores are widely distributed throughout the world, although more than 40 percent of the world's output originates in North America and Australia. The common zinc-containing minerals are the zinc sulfide known as zinc blende or sphalerite (ZnS), a ferrous form of zinc blende known as marmatite [(ZnFe)S], and a zinc carbonate …
Iron ore processing is a complex and vital process that transforms raw iron ore into usable steel. From exploration and extraction to grinding, beneficiation, and ironmaking, each stage plays a crucial role in producing …
The Ore Extraction and Refining Process Before iron ore can be used in a blast furnace, it must be extracted from the ground and partially refined to remove most of the impurities. ... Either way, the fundamental activity in iron making involved a worker stirring small batches of pig iron and cinder until the iron separated from the slag ...
Study with Quizlet and memorize flashcards containing terms like Explain the basic process of making steel?, Explain the blast furnace and process?, List the different types of iron ore? and …
حقوق النشر © 2024.Artom كل الحقوق محفوظة.خريطة الموقع