Iron Ore Pelletization Technology and its Environmental …
Agglomeration technologies such as Pelletization / Sintering have to be added to Steel Plant so that concentrates can be used as feed material. This paper will give an insight …
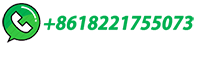
Agglomeration technologies such as Pelletization / Sintering have to be added to Steel Plant so that concentrates can be used as feed material. This paper will give an insight …
Pelletization is the process of making spheres of uniform quality iron ore with high carbon content. Iron ore is pelletized so that it can efficiently flow through a blast furnace for smelting. The process involves mixing iron ore fines with …
As the world leader in tumble growth agglomeration, FEECO provides a variety of services and equipment for iron ore pelletizer plants. As the needs of the steel industry change, one production component looks to be increasingly important in meeting the needs of the modern steel industry: iron ore pelletizing. Iron ore pelletizing, or balling, is the process of transforming fines into …
Also focus on the present status of iron ore reserves in India, inventory of iron ore pelletization plant, primary data collection by conducting field monitoring for air, water and solid waste ...
Pelletization is a process in mining operations through which iron ore fines are transformed into an agglomerated form called iron ore pellets. ... plants and automation solutions for aggregates production. ... Pelletization is the process of transforming iron ore fines into spherical pellets through agglomeration and induration. These pellets ...
The iron ore pelletizing process mainly includes preprocessing (preparation of high-quality iron fines), mixing (preparation of raw materials), and pelletizing(balling). How to Pelletize Iron Ore? (The Complete Guide)
Pelletizing is the process of converting very fine iron ores into spheres (normally 8mm-20mm in diameter), known as pellets. These pellets are suitable for both blast furnaces and direct iron reduction processes.[1][2] Iron ore pellets are manufactured by mixing beneficiated iron ore fines or natural iron ore fines with additives, then being processed …
With the growing numbers of iron ore pelletization industries in India, various impacts on environment and health in relation to the workplace will rise. ... all de-dusting/scrubber return water is passed and the underflow is reused in the process. The pellet plant has a goal to achieve zero discharge norms with a comprehensive water and waste ...
Therefore, a greater number of pelletizing plants have been set up all over the world having capacity more than 800 million tonnes per annum to utilize iron ore high-grade fines to improve the conservation of iron ore in the world. During pelletization process and preparation of feed for DRI or reduction smelting processes, around 3% of pellet ...
ABSTRACT The behavior of iron ore pellet binders is complex. Any pellet binder is subject to a handful of practical requirements: that it be readily dispersed through a pellet, that it effectively controls the movement of water within the pellet, and that it contributes to the inter-particle bonding within the pellet. Meeting these requirements leads to the formation of strong …
The document summarizes the key steps in the iron ore pelletization process. It describes how iron ore fines and binders are mixed and formed into green balls either using a disc pelletizer or drum pelletizer. The …
The Direct Reduction of Iron. Thomas Battle, ... James McClelland, in Treatise on Process Metallurgy: Industrial Processes, 2014. 1.2.2.2 Agglomeration of Iron Ore. The three major forms of iron used in ironmaking are pellets, lump, and sinter. The major change in the past 50 years has been the development of cost-effective pelletization technology allowing pellets to be a …
An iron ore pelletization plant is a facility that produces iron ore pellets from iron ore fines. The fines are agglomerated into spherical pellets, which are then used in the production of steel. Our plant employs advanced technologies & processes to enhance the properties of iron ore & create pellets that are highly efficient & cost-effective.
Agglomeration is the process of converting iron ore fines into easily handled size and shapes as required in blast furnaces [1]. In the pelletization process, fine materials are rolled with water ...
Better quality wet, dry, preheated, and fired pellets can be produced with combined binders, such as organic and inorganic salts, when compared with bentonite-bonded pellets. While organic binders...
Iron ore pelletization 15 ... The pelletization process is very widely used, particularly when burden materials must be shipped great distances ... 1973). In 1955, two pelletizing plants commenced ...
As high-grade iron ore deposits become more limited, it is necessary to upgrade lower quality iron ore resources through concentration. The ground iron ore must be pelletized prior to feeding into a blast furnace or DRI plant. Our pelletizing equipment is designed to produce pellets of highest quality at the lowest cost.
In an iron ore pelletization plant, pellets are produced inside a rotating disc pelletizer. Online pellet size distribution is an important performance indicator of the pelletization process. Image processing-based system is an effective solution for online size analysis of iron ore pellets. This paper proposes a machine learning algorithm for estimating the size class of …
for the recycling of iron ore wastes in steel plants. 2.3. Extrusion Extrusion is a process widely used in the ceramic industry, but it has begun to be used in the ... Bentonite clay is the most common binder agent in iron ore pelletization as we mentioned previously, and is added at levels of 0.5 1.5% by weight [8]. There are others, that can be
PDF | Iron Ore, Iron Ore Pellets, Direct Reduced Iron )DRI( Pellets, Iron Ore Pellets Market, Pelletizing Process, Sintering, Binder, Induration... | Find, read and cite all the research you need ...
The Direct Reduction of Iron. Thomas Battle, ... James McClelland, in Treatise on Process Metallurgy: Industrial Processes, 2014. 1.2.2.2.1 Pelletization. Pelletization is the most popular method of converting iron ore fines into agglomerates. Early work on pelletization took place in Sweden, but commercialization at large scale first occurred in the United States [13].
The pelletization process is the primary consumer of binders in the iron ore industry. The selection of an appropriate binder type and dosage is of critical importance in producing good quality pellets at a reasonable price. Binders accomplish two …
The iron ore production has significantly expanded in recent years, owing to increasing steel demands in developing countries. However, the content of iron in ore deposits has deteriorated and low-grade iron ore has been processed. The fines resulting from the concentration process must be agglomerated for use in iron and steelmaking. This chapter …
The pelletization process is the primary consumer of binders in the iron ore industry. The selection of an appropriate binder type and dosage is of critical importance in producing good quality pellets at a reasonable price. Binders accomplish two …
Evolution of binders for iron ore pelletizing Induration technologies Challenges and innovations in iron ore pelletizing 2. Pelletizing process and raw materials The iron ore is mined mostly from open pit deposits through mining operations and the raw product, run of mine, is subjected to mineral processing.
Iron ore pelletization is a critical aspect of the steel manufacturing process, providing a method to utilize fine iron ore particles and beneficiate lower grade ores, which enhances the overall …
Iron ore lump, sinter, and pellets comprise the main burden of modern blast furnaces. However, sinter and pellets are now the dominant blast furnace burden, because the nat-ural lump supply...
Iron ore and iron ore pellets are important sources of iron for manufacturing steel. The iron ore production has significantly expanded in recent years, owing to increasing steel demands...
ABSTRACT. The behavior of iron ore pellet binders is complex. Any pellet binder is subject to a handful of practical requirements: that it be readily dispersed through a pellet, that it effectively controls the movement of water within the pellet, and that it contributes to the inter-particle bonding within the pellet.
Iron ore pelletization is a critical aspect of the steel manufacturing process, providing a method to utilize fine iron ore particles and beneficiate lower grade ores, which enhances the overall output and efficiency of steel production processes. Pelletization involves converting iron ore fines into compact pellets, which are then used in blast furnaces or direct reduction iron processes ...
حقوق النشر © 2024.Artom كل الحقوق محفوظة.خريطة الموقع