Implementation of industrial waste ferrochrome slag in …
Cold crushing strength (CCS) is the capacity of a material to withstand axially directed pushing forces. Cubic test specimens of 50 mm size were prepared and the value of maximum uniaxial load (in N) was noted when the sample block failed completely. Finally CCS value was calculated using the method stated in ASTM C133-97 [20].
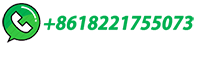