How does a stone crusher work?
Feeding: Large stones are fed into the crusher through a hopper. Primary Crushing: The crusher uses machines like jaw crushers or gyratory crushers that are designed to take large chunks of rock and reduce them to smaller pieces. This stage involves compressive forces where the jaw plates or gyratory cones exert pressure, causing the rock to ...
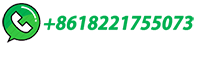