Iron Ore Pelletizing Process: An Overview
ISO 4700 Determination of the crushing strength. ... In the first stage, the hot air from the co oling zone is blown from the bottom. ... Iron Ore Pelletizing Process: An Overview ...
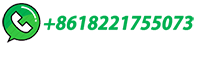
ISO 4700 Determination of the crushing strength. ... In the first stage, the hot air from the co oling zone is blown from the bottom. ... Iron Ore Pelletizing Process: An Overview ...
Due to differences in ore properties, different processes and equipment are used in iron ore dressing, but most iron ore processing processes need to go through the following stages. The large iron ore is fed into the jaw crusher by the …
Mining of iron ore is a highly capital- and energy-intensive process. Life cycle assessment (LCA) of the mining and mineral processing of iron ore in Australia was carried out in this chapter ...
Iron ore handling, which may account for 20–50% of the total delivered cost of raw materials, covers the processes of transportation, storage, feeding, and washing of the ore en route to or during its various stages of treatment in the mill.. Since the physical state of iron ores in situ may range from friable, or even sandy materials, to monolithic deposits with hardness of …
Characteristics of rock chrome ore process. Mining method: Rock chrome ore is usually embedded in solid rock, and the mining process may involve deeper excavation, blasting, and crushing operations. Main process: Rock chrome ore processing often requires crushing and grinding to reduce the ore's particle size. Since chromite may be enclosed in other minerals, …
Crushing is the initial stage in the iron ore processing journey, where large chunks of ore are broken down into smaller fragments. The primary objective of crushing is to reduce the ore size for subsequent processing and …
Before being crushed, the iron ore must first be broken up to an F 80 grind size. The crushed ore is then sent to a stockpile after being crushed.
The processing and production technology of copper ore mainly includes three processes: crushing, grinding, and beneficiation.The modern copper ore crushing method adopts three-stage closed-circuit crushing, which can not only complete the crushing and partial dissociation of the ore, but also improve the efficiency of subsequent grinding.During the …
Iron ore pre-treatment equipment. The pre-treatment stage of iron ore mainly includes crushing, screening, grinding, and grading processes.. Crushing and screening: The raw ore is sent to the crusher by the vibrating feeder, and the crushed product enters the screening machine. The materials on the screening return to the crusher for further crushing, and the …
Request PDF | On Oct 1, 2023, Lage Wivyan Castro and others published Tribological study of fourth-stage crusher coatings applied in an iron ore processing plant | Find, read and cite all the ...
Due to the decreasing reserves of high-grade iron ore and secondary resources used for steelmaking, it has become an important research and development area to improve the grade of iron ore through crushing (Gul et al., 2014).The quality of iron ore crushing directly affects the performance of pellets and sinter, so as to influence the quality and performance of …
Main properties of the processes of iron ore destruction in terms of its simultaneous effect by mechanical load and electric field of ultra-high frequency have been studied.
The first stage: crushing and screening, three-stage closed-circuit crushing. Large pieces of iron ore are evenly sent to the jaw crusher or coarse crushing mobile station through …
In medium and small iron ore concentrators, two-stage crushing processes are generally used. This process can be used when the size of the raw ore is small or the required crushing is small. If the granularity of the crushed …
The processed ore size defines the type and position of each stage. For instance, the primary crushing stage receives the extracted iron ore directly from the mine, where the iron ore diameter may reach 1 m. In the quaternary crushing stage, the size of the ore that feeds the crushers is less than 20 mm. Screens classify the ore by size and ...
Crushing is an versatile process and the kind of crusher you need depends on the 'stage' of crushing. The three main stages of crushing are primary, secondary, and tertiary - all of which have their own unique benefits. ... like a jaw crusher …
What Are the Stages of Rock Crushing? Rock crusher machines are a key tool in mining and construction operations. These machines operate within a few different stages: Primary Crushing. In this stage, rock crushers such as jaw crushers are used to reduce the size of large rocks into smaller rock particles for easier processing. This typically ...
Mine rock ore crushing: iron ore, copper ore, gold, lead-zinc, coal, manganese ore, silica sand, etc. Solid waste recycling and crushing stage: tailings, slag, construction waste, etc. Inquiry Now. Fixed Rock Crusher For Sale Rock crushing equipment and crushers are essential for construction, mining and mineral processing. Its main function is ...
Iron ore has a special place in the global mining industry, judging by the volumes of ore processed and the energy usage. It is very well known that energy production also implies emission of CO2, as shown in Figure 1 (). ... stage crushing followed by primary and secondary milling. Primary crushing followed by wet SAG or ...
The crushing process of magnetite often adopts a continuous flow of two-stage and one closed-circuit crushing. 1 The raw magnetite ore is sent to the coarse crusher ( jaw crusher ) by the vibrating feeder, and then sent to the fine crusher ( cone crusher or hammer crusher ).
Iron ore must go through a lengthy pre-processing stage before it can be pelletized – a series of steps that work to beneficiate and concentrate low-grade ores. This process varies depending on the ore source, but typically involves various stages of crushing and grinding to …
Ore arriving at the crusher from the distant mines is again stockpiled in preparation for blending into the crusher, which reduces the ore particle size to produce two distinct products, lump and fines, each having to closely match their different tar-get compositions, not only in iron but also in phosphorus, silica, and alumina.
The first stage: crushing & screening – three stage closed-circuit crushing Large pieces of iron ore are uniformly sent to the jaw crusher or coarse crushing mobile station by the vibrating feeder for coarse crushing; the coarsely crushed iron …
The primary crushing stage reduces the very large size of crude iron ore to around 150 mm and further down in subsequent crushing stages to the size of calibrated iron ore (-40 mm to +10 mm), CLO, as the final product. The crusher product is fed to the milling operation for further size reduction when subsequent processing of ore is needed.
The processing of iron ore mainly goes through the processes of crushing, grinding, beneficiation, and drying, among which the crushing process is the primary and important link in iron ore processing.
Due to differences in ore properties, different processes and equipment are used in iron ore dressing, but most iron ore processing processes need to go through the following stages. The large iron ore is fed into the jaw crusher by the vibrating feeder through the silo for preliminary crushing. After reaching a certain particle size, it enters ...
Iron processing, use of a smelting process to turn the ore into a form from which products can be fashioned. Included in this article also is a discussion of the mining of iron and of its preparation for smelting. Iron (Fe) is a relatively dense …
The iron ore processing industry produces usable concentrations of iron-bearing material by removing nonferrous rock (gangue) from low-grade ore. In the United States, predominant iron ore is taconite which is a hard, banded, low-grade ore. Ninety-nine percent of the crude iron ore produced in the United States is taconite.
When dealing with argillaceous iron ore with high water content, or when restricted by terrain conditions, a three-stage open-circuit crushing and rod mill crushing process is sometimes used. That is to relax the particle size of …
The crushing method is selected depending on the properties (viscosity, strength, elasticity) of the rocks, to achieve the greatest crushing efficiency. For example, for strong and non-brittle …
حقوق النشر © 2024.Artom كل الحقوق محفوظة.خريطة الموقع