Tests of Briquettes for Mechanical Strength
of cast iron in the ore portion of blast-furnace charges was achieved with briquettes that displayed a strength of 70 to 75% (the fraction of particles larger than 5 (6.3) mm) in the t umbler test ...
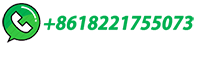
of cast iron in the ore portion of blast-furnace charges was achieved with briquettes that displayed a strength of 70 to 75% (the fraction of particles larger than 5 (6.3) mm) in the t umbler test ...
1.1 This test method describes a method for determining the crushing strength of fired iron ore pellets and direct-reduced iron. Cylindrical agglomerates and briquettes are not covered by this test method.
Iron ore pellets are the raw materials for direct reduction process of iron ore to sponge iron pellets and is an important step in the iron and steel production chain.
Crush strengths ranged from 200 kgf to >450 kgf. 1. Introduction. At present, around 460 mt/a of unprocessed hematite-goethite iron ore fines are exported from Australia as they are …
The mechanical properties of briquettes from iron ore concentrate with coke screenings, presented in the form of analytical dependencies, are necessary to assess the strength of the briquettes ...
E382 – 12 Standard Test Method for Determination of Crushing Strength of Iron Ore Pellets, … briquettes, and reduced pellets are not covered by this test method. » More detailed!
Iron ore briquetting: a Brazilian innovation. The briquette products are pressed from high-quality iron ore at low temperatures using a binder technology solution, resulting in a final product with high mechanical strength. Vale announced in 2021 that it would launch briquetting products.
DOI: 10.1016/J.FUPROC.2018.01.006 Corpus ID: 102892784; Effect of iron ore type on the thermal behaviour and kinetics of coal-iron ore briquettes during coking @article{Xu2018EffectOI, title={Effect of iron ore type on the thermal behaviour and kinetics of coal-iron ore briquettes during coking}, author={Runsheng Xu and Bo-wen Dai and Wei Xiang Wang and Johannes …
Vale is working to increase its production of high-quality iron ore and expand its capacity to concentrate ore, which also raises the iron ore grade, enabling the company to meet demand from steelmakers for these products. Product in expansion. Vale is building two 6mtpy briquette plants at its Tubarão Unit in Vitória, Espírito Santo, Brazil.
The influence mechanism of basicity on the reduction swelling index (RSI) of iron ore briquettes was investigated using the SEM analysis and Factsage 7.3 thermodynamic calculations based on the addition of pure CaO to Bayan Obo iron concentrate. The results revealed that the solid solution of Ca 2+ in the FeO lattice increased with the basicity of the briquettes, whereas the …
Coke acts as a reducing agent, spacer, and heat source, and its strength is important for stable operation of a blast furnace.1,2) In recent years, utilization of high-reactivity coke has been necessary to enhance the efficiency of blast furnace operations with effective use of carbon resources.3,4) Highreactivity coke has received substantial attention because its use …
Another way of improving the agglomerate strength is by producing iron ore coal briquettes by hot pressing. The fluidity phenomenon of coal at temperature 350–600 °C can be utilized in gaining high density and high strength without the addition of any binding materials (Matsui et al. 2003). Utilization of thermal plasticity of coal is being ...
Iron ore pellet sample supplied by a domestic pelletizing plant (China) was used in this work. The elemental composition of iron ore pellets is shown in Table 1. And the charged pellets were in the size range of 12.5–16 mm with average crushing strength of 2973 N/pellet.
The higher strength of directly reduced iron (DRI) in pellet form is useful in handling, storing and charging from height without breakage. The DRI pellets commonly exhibit 60 kg cold crushing strength. In this work the effect of reduction temperature, sintering time, quantity/quality of additives and manner of reduction by solid reductant has been studied. The …
The slag ing caused by Ti(C,N) is the main limitation of smelting vanadium–titanium magnetite by blast furnace. COREX, with unique pure oxygen injection that avoids the formation of Ti(C,N ...
and crushing strength of briquettes. Briquette Peak Weight loss Crushing Heat. number temperature ( wt%) ... It was developed and used in the production of iron ore pellets in China. In this paper ...
Apart from these wastes large quantity of iron ore fines are generated during mining, crushing and grinding. Most of them are in fine fraction and difficult to use even for making sinter use as a feed ... 2.2 Mechanical strength of briquette and lumpy iron ore . The mechanical properties of briquette and iron ore are given in table 6. The cold ...
Iron ore handling, which may account for 20–50% of the total delivered cost of raw materials, covers the processes of transportation, storage, feeding, and washing of the ore en route to or during its various stages of treatment in the mill.. Since the physical state of iron ores in situ may range from friable, or even sandy materials, to monolithic deposits with hardness of …
strength is the maximum crushing load a briquette can . ... The mechanical strength of the briquettes was determined by the drop test and compression test methods, while a bomb calorimeter was ...
Twenty different iron ore pellets, consisting primarily of Hematite (Fe2O3) phase, were subjected to 'simulated' reduction studies. A wide range of reduction time periods, Rt of 122 to 211 minutes, were obtained. Detailed microstructural characterizations were then conducted at different locations of ten selected specimens. The Rt did not relate with initial phase mix or …
content, particle size, and residence time on the tensile crushing strength, impact resistance, and water resistance of the briquettes; it was found that the tensile crushing strength of the briquettes increased from less than 40 kPa to more than 800 kPa in the weakest (longitudinal) orientation after adding starch as binder. Hu et al
In the experiments, 3KN (~24.5 MPa) force was applied to compress iron ore fine into a compact with a relative density of 0.86, which is a typical value for briquettes. In the …
BCB kept a crushing strength after partial reaction of more than 1900 N/briquette through the whole testing period and reached a maximum strength of 5500 N/briquette at 1473 K (180 min). Generally, the briquette kept a permittable crushing strength after partial reaction that is required for practical blast furnace iron-ore bearing burden in ...
High-quality iron ore is agglomerated at low temperatures to create the briquette, which is then finished off with a binder technology solution to give it a high mechanical strength. In a press statement, Vale said: "The product also reduces the emission of particulates and gases such as sulphur dioxide (SOₓ) and nitrogen oxide (NOₓ), as ...
The briquettes exhibited significant strength loss when heated in the nitrogen atmosphere due to the destruction of the bonding matrix. Strength loss became even more drastic when heating took ...
Hot Briquetted Iron (HBI) is the densified briquette form of Direct Reduced Iron (DRI). DRI is discharged hot from the reduction furnace and screw-fed into the nip between two counter …
The mechanical properties of briquettes from iron ore concentrate with coke screenings, pre- sented in the form of analytical dependencies, are necessary to assess the strength of the …
1.1.3.2.1.2 Iron-Bearing Materials. Ore fines and iron concentrates make the main part of the sinter mix. The grain size of ore fines and concentrates is typically 0–8 and 0–3 mm, respectively.Grains smaller than 0.1 mm are not desired because they reduce the gas permeability of the bed and thus decrease the sintering efficiency.Recycled materials, such as …
In Part 1, we went back to the basics and described what is Hot Briquetted Iron (HBI), what makes it such a useful source of steelmaking metallics, how it became part of MIDREX® Direct Reduction Technology, and where HBI …
Quicklime briquette can be used to replace the lime block to smelt the calcium carbide in the production of calcium carbide. Lime briquette is used in steel manufacturing as a fluxing agent to remove impurities from the iron ore. It can be used as a good desulfurized material during steel-making production. 5. Gypsum briquette machine
حقوق النشر © 2024.Artom كل الحقوق محفوظة.خريطة الموقع