11.6 Portland Cement Manufacturing
11.6 Portland Cement Manufacturing 11.6.1 Process Description1-7 Portland cement is a fine powder, gray or white in color, that consists of a mixture of hydraulic cement materials comprising primarily calcium silicates, aluminates and aluminoferrites. More than 30 raw materials are known to be used in the manufacture of portland cement, and these
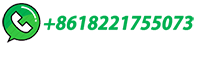