Working principle of ball milling process.
In the past few decades, many researchers studied on different extraction methods to overcome high energy demand and clogging issues associated with homogenizers such as grinding, microfluidizing ...
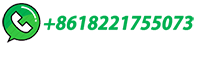
In the past few decades, many researchers studied on different extraction methods to overcome high energy demand and clogging issues associated with homogenizers such as grinding, microfluidizing ...
These centrifugal forces operate on the powder mixture and the balls, resulting in fracturing and cold welding of the powder mixture. The milling balls can attain impact energies of upto 40 times more than that caused by the gravitational acceleration, in normal directions. Thus, planetary ball milling can be employed for high speed/energy milling.
Specification of high energy ball mill: • Principle: Milling to be done using friction and repeated impact of shots and balls. • Applications: Mechanical alloying, homogenization, size reduction, colloidal grinding. These application are the domain of chemistry, civil engineering, recycling of wastes, metallurgy, mining, chemicals, ceramics, and oxides etc.
High energy ball milling exerts higher kinetic energy (~30 mJ) refers the impact of a single ball collision that is traveling with a velocity of at least 3.6 m/s. than the conventional ball ...
The MM 500 control is a high energy laboratory ball mill that can be used for dry, wet and cryogenic grinding with a frequency of up to 30 Hz. It is the first mixer mill in the market that allows to monitor and control the temperature of a grinding process. The temperature area covers a range from -100 to 100 °C.
a milling process. High Energy and Reactive Milling is performed by the same processing principle where the variation is in general based on the target of processing, the transformation effect of kinetic and the starting materials. The various procedures can be described as high kinetic processing where the collision of grinding media is the ...
Ball mills are one of the more common mills and use a closed cylindrical container that is rotated horizontally on its axis so that the media cascades. A typical ball mill has an L/D ratio of 1.5:1. Ball mills are filled with spheres or other shapes made of steel or ceramics; or with pebbles made of flint (or of an ore being ground).
The working principle of a ball mill is based on the impact and attrition between the balls and the grinding media. As the mill rotates, the grinding media (usually steel or ceramic balls) are lifted to a certain height and then allowed to fall freely, causing the materials to be reduced in size by the impact and abrasive forces generated ...
The basic principle of a ball mill is very ancient. However, the machine itself could be produced only after the industrial revolution. Typically, ball mill is a grinder and is often employed blend materials by ... Despite these limitations, high energy ball milling is extensively used due to simple design, working, and use to provide finely ...
In this paper, the milling parameters of high energy ball mill (Fritsch Pulverisette 7) like vial geometry, number and size of balls and speed of the mill were modelled and discussed. Simulations through discrete element method (DEM) provide correlation between the milling parameters. A mathematical model is used to improve and develop this ...
It works on the principle of impact and attrition, where balls drop from near the top of the shell as it rotates to grind materials placed inside. ... replaced by new ones so that mill contains balls of various ages. Ball mill produces 1 to 50 ton/hr of powder and energy requirement of the ball mill is about 16 kwh/ton. ...
As the cylinder starts to rotate, the grinding balls inside the cylinder crush and grind the feed material, generating mechanical energy that aids in breaking bonds, activating the catalyst, and ...
High-energy ball milling is a mechanical deformation process that is frequently used for producing nanocrystalline metals or alloys in powder form. This technique belongs to the comminution or attrition approach introduced in Chapter 1.
Our high energy ball milling process operates dry and under an inert environment to prevent oxide formation and eliminate contamination associated with process control agents. High energy ball milling can be applied anywhere from the …
Ball milling process is a mechanical process which relies on the energy released at the point of collision between balls as well as on the high grinding energy created by friction of balls on the ...
PLANETARY BALL MILL WORKING PRINCIPLE. ... They generally are available in three different sizes of 80, 250 and 500ml. For high energy mechanical alloying, however, steel bowls are recommended since ceramic bowls can cause contamination due to minute chipped off or fractured particles from the brittle surfaces of the milling bowl and balls ...
In this paper, the milling parameters of high energy ball mill (Fritsch Pulverisette 7) like vial geometry, number and size of balls and speed of the mill were modelled and discussed.
Ball milling is a mechanical process that involves the rotation of a drum containing grinding media, typically steel balls, at a high speed. The materials to be milled are loaded into the drum, and as the drum rotates, the grinding media collide with the materials, causing them to …
work [17]. 2.2 Instrument . The high-energy planetary ball mill [18] fabricated by German Fritsch Company (type Pulversiette 7) was used in the simulation. This mill consists of a rotating support disk (called turn table) and two milling vials, as presented in Fig. 1. Fig.1. Pulverisette 7 planetary ball mill and vials used in experiment.
It has been reported that the impact energy of HEBM is typically 1000 times higher than the conventional ball milling energy. 43 The major use of the conventional ball milling is to fracture the particles and to reduce the size, while in high energy ball milling, a longer milling time can be achieved, which can help to activate and complete the ...
These work on the mechanics of rotation and make the process of mixing go by smoothly and efficiently. There are different equipment that is used to make an efficient high-energy ball mill because the equipment involved is rich in its characteristics and enables a better working ... Emax's Working principle. For high-energy milling, Emax is a ...
Ball milling: The main principle of mechanical milling can be described as the exploitation of high energy grinding to reduce the particle size. In general, the high energy ball milling route is …
In order to evaluate the results obtained after high-energy ball milling and pyrolysis of these milled powder mixture, milling parameters have been converted to two energy parameters, namely ...
Nanocrystalline powder of the CoCrFeNiAl high-entropy alloy was produced by high-energy ball milling (HEBM) and consolidated by spark plasma sintering (SPS). Microstructure and crystal structure transformations occurring in the …
The high-energy ball mill processing can be divided in three main groups according to the mechanisms involved and/or the purpose envisaged: Mechanophysical conditioning, Mechanochemical...
The main advantage of high-energy mechanical ball milling is that in one step, it can produce a large quantity of metal hydrides with desired properties [212, 272, 317, 318]. Ball milling is generally done under an inert gas environment because metal hydrides are sensitive to air and water. ... works as an efficient heat conductor, has better ...
The current production method of nanobiochar (NBC), an emerging, environmentally friendly nanocarbon material, is tedious and lengthy. Therefore, in this study we aimed to improve the productivity of NBC via high …
A Ball Mill is a type grinder that blends or grinds materials for various applications. Impact force enables size reduction in feed material. The cylindrical shell rotates around its horizontal axis. The main element enabling grinding are the hard and small balls in the ball mill. These balls are usually made of steel.
The high-energy ball mill processing can be divided in three main groups according to the mechanisms involved and/or the purpose envisaged: Mechanophysical conditioning, Mechanochemical synthesis and mix processes.
The lack of shrouding allows the use of a water jacket on the tank in an internally agitated ball mill, providing cooling or heating to aid in the grinding process. Unlike planetary ball mills, Attritors offer the advantage of being able to sample the material during milling without having to stop the process. Formulation adjustments and grind ...
حقوق النشر © 2024.Artom كل الحقوق محفوظة.خريطة الموقع