Study of the Energy-Power Parameters of the Crushing …
In the process of crushing, the drive is subject to the following: the crushing force torque at a free strike of the hammer on a piece of material Mstrk, the friction forces torque arising from the …
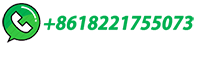