Ball Mill
But at 2/3rd of the speed (50 to 80% of the critical speed), Fig.1(c), the centrifugal speed force just occurs with the result that the balls are carried almost to the top of the mill and then fall to the bottom. In this way, the maximum size reduction is affected by the impact of particles between the balls and by attrition between the balls. ...
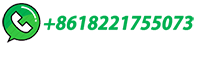