AMIT 135: Lesson 5 Crushing – Mining Mill Operator Training
The purpose of the primary crusher is to reduce the ROM ore to a size amenable for feeding the secondary crusher or the SAG mill grinding circuit. The ratio of reduction through a primary crusher can be up to about 8:1. Feed: ROM up to 1.5 m; Product: -300mm (for transport) to -200mm (for SAG mill) Feed Rate: 160 to 13,000 tph
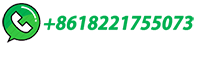