Recent progress on research of molybdenite flotation: A …
Molybdenum is an important alloy element for metallurgical industry because of its high temperature stability. As the major mineral reserve for molybdenum, molybdenite (MoS 2) is commonly found in porphyry copper deposits.Molybdenite is naturally floatable and can be separated from copper sulfide mineral using froth flotation.Properties of molybdenite such as …
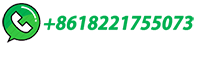