Improving Productivity and Energy Efficiency in Copper …
Copper Electrowinning Plants Eduardo P. Wiechmann, Senior Member, IEEE, Anibal S. Morales, and Pablo Aqueveque, Member, IEEE Abstract—This paper presents strategies to improve energy
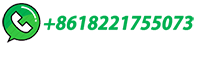
Copper Electrowinning Plants Eduardo P. Wiechmann, Senior Member, IEEE, Anibal S. Morales, and Pablo Aqueveque, Member, IEEE Abstract—This paper presents strategies to improve energy
Reaction for Copper Electrowinning Gerald L. May Bill Imrie Sharon Young Brent Hisky Jan Miller Michael Free July 2005 . INL/EXT-05-00539 ... the immediate vicinity of the electrowinning plant for leaching of additional copper. Excess acid is only consumed with the leaching of oxidized copper minerals in alkaline host rock. Host rock in the
Sichuan Precision Technology (PRS) recently completed the production of essential equipment for a copper electrowinning plant designed for a customer in Southeast Asia. To ensure that all components met stringent quality standards, a dedicated inspection team was dispatched to the manufacturing facility. Over the course of three days, the team ...
Electrowinning is used to purify metals, such as zinc, copper, tin, nickel, cobalt, magnesium, PGMs and Rare Earths.Even aluminium, chlor-alkali and green hydrogen are debatably electro-winning processes, or at the least electro-chemical processes whose energy economics can all be modeled using Faraday's Law of electrolysis.. Electrorefining of metals was developed in the …
Figure 4: Copper cathode obtained after electrowinning process (a) front (b) back (c) side, and (d) electrolyte solution before (left) and after (right) electrowinning. amount of copper deposited at the cathode and greater recovery of copper were obtained as the cell voltage was increased from 2.2 to 2.6 V, due to increasing current with ...
Electrowinning comprehensive scope of supply. is the right partner for building an efficient, productive, and safe electrowinning plant with optimized cathode and cell sizes, current densities, busbars, and an automatic material flow of cathodes. We offer full technology and equipment package with proprietary of whole electrowinning ...
The suitability of CIP technology for the West Driefontein Reclaim plant was investigated using a pilot plant pump-cell supplied by Kemix The data gathered were utilized in sizing a full scale AAC ...
"The integrated Copper Electrowinning Plant produces high-purity cathodes and offers proven reliability and availability by leveraging modern, proven technology. Its advanced digital and automation solutions and the acid …
Process metallurgist at kansanshi Mine solwezi · I am a metallurgist with professional experience in Concentrator, Leach Plants,Solvent Extraction and electrowinning plants. · Experience: First Quantum Minerals LTD · Education: University of Zambia · Location: Solwezi · 500+ connections on LinkedIn. View Justin Masapi's profile on LinkedIn, a professional community of 1 billion …
Copper SX-EW technology Benefits • High process performance • State-of-the-art process technologies • Project and plant optimization • High availability and working ergonomics • Maximum safety and environmental hazard control Our solution for leaching, solvent extraction and electrowinning
The refinery uses the ISA process and was commissioned in mid-1988 with a capacity of 51kt/a refined cathode. Electrowinning of copper from leach solutions is also undertaken in the same plant and, at commissioning, electrowinning used one half section of the installed eight 32 cell sections. In 1992...
Electrowinning is used to purify metals, such as zinc, copper, tin, nickel, cobalt, magnesium, PGMs and Rare Earths.Even aluminium, chlor-alkali and green hydrogen are debatably electro-winning processes, or at the least electro …
Large scale electrowinning of copper was developed between 1912 - 1915 at Chuquicamata in Chile. As the industry grew to meet the consumer demands there were steady improvements …
The improvement in the leaching and solvent extraction technologies continues to increase the importance of copper electrowinning into the word of copper production. The quality of copper deposit has been improved dramatically by the introduction of the permanent cathode technology. The paper gives a method of designing the copper electrowinning circuit of a plant having …
The first zinc and copper electrowinning plants operating at the beginning of the century did not use acid mist suppression methods. No s were used and operators would typically have to wear clothes and cloth over the face to protect them trom the mist [1]. The zinc industry was first to develop electrolyte-based surfactants on a large ...
copper, 15 of which accounted for 99% of production. Three smelters, 3 electrolytic refineries, 4 fire refineries, and 14 electrowinning facilities operated during 2019. Refined copper and scrap were used at about 30 brass mills, 15 rod mills, and 500 foundries and miscellaneous consumers. Copper and copper alloy products were used in building
In other news at , the company has introduced its new integrated copper electrowinning plant. Subscribe to Australian Mining and receive the latest news on product announcements, industry ...
Cyanidation has been used to extract gold (and silver) from ores, concentrates, and calcines since the 1890s. The precipitation of gold from cyanide solutions by zinc cementation was patented in 1884 and was applied industrially as early as the cyanidation process.
"When the CuEW Plant is integrated with SX plants, high quality and production can be ensured." Electrowinning is used to recover metals from concentrated solutions by applying …
Copper ore leaching and electrowinning pilot plant includes the ore leaching tank, slurry filtration tank, electrowinning tank, etc. After leaching the copper ore, the copper ion will enter into the liquid, by the electrowinning work, …
generator, electrical energy and copper refining/winning were united in the first electrolytic copper refinery in 1869. A plant for large-scale copper electrowinning from leach solutions was first built in 1917. 1 Since then, although the basic prin-ciples and fundamental theories of copper refining/winning have remained
largest copper electro-winning plants in the DR Congo. 2010 G Corner completes the delivery of DC busbar equipment for its first copper foil manufacturing plant in Malaysia. Awarded a major project for cell top busbars and associated equipment for the largest Nickel EW refinery and base metal refinery in North America.
In copper electro-refining the copper anode and copper deposit on the cathode leach very slowly in electrolyte, and do not set up a galvanic couple. In electrowinning however the copper on the cathode and the lead anode do set up a reverse voltage. The resultant reverse current flow can have dramatic impacts on electrodes and copper product:
has introduced its new integrated copper electrowinning (CuEW) plant, designed to ensure safety and operational sustainability for producing high-purity copper …
An engineering house's perspective of required inputs in designing a copper electrowinning tank house and ancillary equipment calls for both understanding of the key fundamental controlling mechanisms and the practical requirements to optimize cost, schedule and product quality. For direct or post solvent extraction copper electrowinning design, key …
Copper was extracted on asphalt-lined leach pads and recovered in the first solvent extraction and electrowinning (SX/EW) plant in Latin America. Production capacity was 33,000 …
Improving cathode morphology at a copper electrowinning plant b y optimizing Magnafloc 333. ... on the surface roughness of the copper deposit was first validated against the literature. The ...
Multiple elements can be recovered from e-waste, including base metals such as copper (Cu), precious metals such as gold and silver, and critical metals such as palladium and other REEs (Balde et al., 2017).Among them, Cu has accounted for 10–25% of the metal contents in e-waste, which was higher than the Cu content found in raw and ores (Fogarasi et al., …
As a result each mixer settler is ½ the size of those in the 2×1 circuit and the total settler area is only 66.7% of that of the 2×1 circuit. The cost saving is estimated to be about 29% which gives a capital cost of $5.0 million. The electrowinning capital cost is the same for each plant and is based on a copper production of 27.2 tonnes/day.
has introduced its new integrated copper electrowinning (CuEW) plant, designed to ensure safety and operational sustainability for producing high-purity copper cathodes. The pre-engineered ...
حقوق النشر © 2024.Artom كل الحقوق محفوظة.خريطة الموقع