A Visual Guide: Steel Making Process Chart
The main stages of the steel making process flow chart include iron ore extraction and processing, smelting in a blast furnace or electric arc furnace, primary steelmaking in a basic oxygen furnace or through electric arc refining, secondary metallurgy for quality control and adjustment, continuous casting, as well as the final rolling and ...
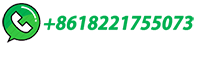