Gypsum Manifacturing | PDF | Gypsum | Nature
Gypsum manifacturing - Free download as PDF File (.pdf), Text File (.txt) or read online for free. This document describes the process of gypsum manufacturing. Raw gypsum ore is mined, crushed, dried, and ground. It is then partially dehydrated through calcination to form calcium sulfate hemihydrate, also called stucco. Stucco can then be used to produce various finished …
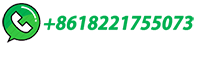