These Copper Oxide Ore Beneficiation Methods Greatly …
30TPH Copper Oxide Beneficiation Methods. This setup is a 30 tph rock copper oxide ore process plant.It is configured with a hopper, feeder chute, hammer crusher, conveyors,fine ore bin, Electromagnetic vibrating feeder,ball mill, hydrocyclone, slurry pump, spiral chute, shaking table and magnetic separator .
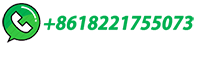