Processing of the Silver–Zinc Crust of the Product of
The pouring of matte from the shaft furnaces was realized after drying the silver–zinc crust directly in the converter. For this purpose, the crust charged into the hot (after the previous cycle of operations) converter was air-blasted at a flow rate of 10,000–12,000 m 3 /h. Then 2–3 ladles of the matte of shaft furnaces were poured into the converter and the …
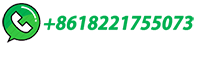