Jaw Crusher
Jaw crushers are mainly used as primary crushers to produce material that can be transported by belt conveyors to the next crushing stages. The crushing process takes place between a fixed …
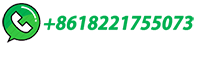
Jaw crushers are mainly used as primary crushers to produce material that can be transported by belt conveyors to the next crushing stages. The crushing process takes place between a fixed …
In this blog post we will explore the mechanics behind crushing materials, looking into its basic operation within a typical jaw crusher. We'll talk about what differentiates it from …
Typical coarse crushing equipment includes jaw crusher, gyratory crusher, and roller-tooth crusher. Ore medium crushing is a process of crushing ore blocks with a feeding particle size of 125–400 mm to 50–100 mm. The maximum crushing ratio of medium crushing is about four. The force in the process of ore crushing is mainly crushing and ...
The Fairmount crusher is inherently a somewhat cleaner breaking machine than either the standard gyratory or standard jaw types, but the class of rock for which the former crusher is largely used is usually subject to greater than average degradation during the blasting and loading operations in the quarry, which tends to level out the ...
Learn everything you need to know about primary crushing, secondary crushing, and tertiary crushing in this comprehensive guide. Discover the types of crushers used in each stage, their working principles, and the …
The jaw crusher is one of the most admired and most sought after equipment from the house of Propel Industries. For the benefit of newcomers in the industry, here is an explainer of the various components of the Jaw crusher. A jaw crusher consists of Crusher Body Pitman Jaw plate Rear end frame Eccentric shaft
There are two main types of primary jaw crushers: single toggle and double toggle. Single toggle jaw crushers are designed with one stationary jaw plate and one movable jaw plate. Double toggle jaw crushers are …
The side frames are deep-welded and then "stress-relieved" in the huge annealing furnaces to eliminate possible failure adjacent to welds. The result is a uniformly strong frame that will remain true during the long service life of the crusher. A jaw crusher frames are of sectionalized construction to facilitate handling.
JW Series Jaw Crusher Enquiry Details 15 When enquiring about the range of ® JW Series Jaw Crushers please supply the following details so that the jaw crusher best suited may be recommended (email or fax this form to your local ® Minerals Processing Systems office). Type of material to be crushed Bulk density of feed material Kg/cu ...
A parameter study using a jaw crusher is designed to investigate the influence of feed gradation, feed rate, crusher setting and crusher speed on the crusher operation and the quality of the produced aggregates. ... The average FI <2CSS for all tests is 11.8, but the FI of the product is considerably different for material above and below CSS.
Introduction: Jaw crushers are powerful machines that are widely used in the mining, quarrying, and recycling industries. These machines are designed to crush large rocks and ores into smaller pieces for further processing. A jaw crusher consists of a fixed jaw and a movable jaw, with the latter being driven by an eccentric shaft that moves the jaw up and down.
CRUSHER SELECTION QUICK GUIDE 1. A typical example of primary crushing is reducing topsize from 900 to 300 mm. 2. A typical example of secondary crushing is reducing topsize from 300 to 100 mm. 3. a typical example of fine crushing is producing concrete aggregates in fractions below 30 mm. 4.
The TJ2440 is a single toggle jaw crusher, designed for tight closed side settings while retaining an aggressive nip angle and crushing stroke resulting in maximum productivity. The below production capacity table supplies the typical expected range of …
Depending on different ways of moving, jaw crushers are divided into four types: Blake jaw crusher, Dodge jaw crusher, PE universal jaw crusher and mobile jaw crusher. …
Typical numbers are for liner and mantles to have a useful wear-life of almost 2,000,000 tonne on abrasive taconite and 9,000,000 tonnes on porphyry copper ores. ... There is less waste or scrap metal coming off a jaw …
A typical jaw crusher can accept boulders that are about 75-90% of the size of its gape (the distance between the jaws at the feed opening), which, for large crushers, can be up to 48 inches wide. Through the use of compressive force, the Jaw Crusher reduces these large boulders into pieces roughly 6 to 8 inches in size.
Jaw Crushers Impact Crushers; Typical rules for primary crusher selection: Rule 1: Always use a jaw crusher if you can due to lower costs. Rule 2: For low capacity applications, use jaw crusher and hydraulic hammer for oversize. Rule 3: For high capacities, use …
The Dodge jaw crusher has a variable feed area and a fixed discharge area, which leads to choking of the crusher and is not ideal for hard materials. Construction and Design: The Blake jaw crusher consists of a heavy-duty frame that carries a fixed jaw and a movable jaw. The movable jaw is pivoted at the top and is moved back and forth by an ...
It will take six months to excavate, install, and commission an underground crusher station for a typical jaw crusher. For a very large jaw crusher or a gyratory crusher, it can take nine months. Source: Jim Redpath; The desired grizzly opening for an underground jaw crusher is equal to 80% of the gape of the crusher. Source: Jack de la Vergne
Comminution is the process by which mined ore is reduced in size to make for easier processing. The strict definition is 'the action of taking a material, specifically mineral ore, and reducing it to minute fragments or particles'. This is typically achieved in several stages of a detailed and …
Jaw crushers are generally defined by their opening size. For example, a 900x650 mm crusher refers to a crusher with an inlet measuring 900 mm by 650 mm. The main parts and main technical parameters of a jaw crusher are …
typical jaw-crusher grinding 3-20 tons per hour costs US$ 20-50,000 for equipment (MachineRoll, 2008); plus US$ 20,000 for working shade, concrete foundation and pur-chase of 25-50 Hp prime movers. Due to high capital cost the technology it is not very affordable in developing countries like Tanzania. As a result, there have been at-
The jaw crusher diagram is instrumental when it comes to adjustments for altering the granularity of the output. One critical metric is the Closed Side Setting (CSS)—the smallest gap between the jaws during the crushing cycle. Adjusting CSS is a straightforward affair and can make a significant difference in your output's size and quality.
Each crusher is designed to work with a certain maximum size of raw material, and often delivers its output to a screening machine which sorts and directs the product for further processing. Typically, crushing stages are followed by milling stages if the materials need to be further reduced. Typical commonly used crushers: · Jaw Crusher
Understanding the technical data of jaw crusher is essential for making informed decisions in mining and construction projects. By considering dimensions, capacity, crushing …
JAW CRUSHER QJ341+ JAW CRUSHER KEY SPECIFICATIONS DATA Equipment Single toggle C12 jaw crusher Feed opening 1.20 m x 750 mm / 47" x 29" Maximum feed size 650 mm³ / 25.6 inch³ Engine C9.3B Stage 5 / T4F 280 kW / 375 hp C9 T3 261 kW / 350 hp NR4 (China) 280kW / 375hp Transport dimensions 14.72 m / 48' 3" (l) 2.79 m / 9' 2 ...
Crushers are needed in a lot of industries for the sole purpose of size reduction. They are invaluable machines in laboratories (whether for institutions, government or private owned), mining and ...
Discover the most common types of jaw crushers used in the stone crushing industry, including single toggle, double toggle, Blake, and Dodge jaw crushers. Learn about their construction, working principles, advantages, …
There are three main types of jaw crushers: single-toggle jaw crushers, double-toggle jaw crushers, and hydraulic jaw crushers. Each type has its own unique features and benefits, making it important to choose the right …
The hydraulic jaw crusher is ideal for crushing hard and abrasive materials, and it is commonly used in mining, metallurgy, building materials, and chemical industries. One of the advantages of a hydraulic jaw crusher is its ability to adjust the discharge opening easily, allowing for a wider range of output sizes.
حقوق النشر © 2024.Artom كل الحقوق محفوظة.خريطة الموقع