Manganese Ore Processing
The Manganese Ore Processing Plant Crushing and Sampling of Manganese Rock. The flowsheet incorporates a conventional multistage crushing plant with a grizzly or screen ahead of both the primary and secondary …
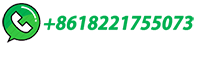
The Manganese Ore Processing Plant Crushing and Sampling of Manganese Rock. The flowsheet incorporates a conventional multistage crushing plant with a grizzly or screen ahead of both the primary and secondary …
Methods Pilot-Scale Sinter Pot Tests. The pellet-sintering process for manganese ore fines includes additional steps of raw material pretreatment and pelletizing, and it employs the technique of fuel fractionation as shown in Fig. 1b. First, the manganese ore fines are finely ground to − 0.074mm accounted for 60% by the roll crusher (Φ200 × 125, 1.2 kW/h) and the …
In the case of lithium ore, ball milling can improve the crystallinity, particle size distribution, and surface area of the ore. ... Lepidolite is distinctive for its pink to purple color, caused by the presence of manganese. It is also a source of rubidium and cesium, which are valuable in specialized applications. 3). Petalite.
Moreover, it offers easy operation, control, and adaptability, making it suitable for various manganese ore separation scenarios. Manganese Mineral Processing Flow: Manganese ore washing and screening: This involves hydraulic flushing or additional mechanical scrubbing to separate the ore from clay soil. Gravity separation process: Suitable for ...
Before gravity separation, the manganese ore is first crushed (6-0mm or 10-0mm) and then classified. The coarse-grained manganese ore particles enter the jig for sorting; the fine-grained ore particles are sent to the shaker for sorting. Commonly used equipment includes gravity separators, spiral separators, etc.
Manganese ore beneficiation is extracting valuable minerals and removing impurities from manganese ore. It usually includes crushing, grinding, washing, gravity separation, …
Much of the surrounding area was mined for iron ore from the 1840s. After the Etowah Iron Company took possession in 1888, it was worked for both iron and manganese. An elaborate manganese mill was built by the Etowah Co. in 1891. The property was sold to the Blue Ridge Mining Co. in 1900, and later, to the local Etowah Development Company.
Manganese ore processing plants typically include crushers, ball mills, screens, and magnetic separators to increase the productivity of mining operations.
The grinding and grading stage of lithium ore is to ensure that lithium minerals are fully dissociated from gangue mineral monomers. Therefore, lithium ore extraction is inseparable from ore grinding, and the common equipment for lithium ore grinding is ball mill. One-stage closed-circuit grinding and grading process can be adopted, and the one-stage grinding …
Manganese ore beneficiation plant can greatly upgrade manganese ores like manganese oxide ore, manganese carbonate ore, iron manganese ore, and polymetallic composite manganese ore. ... Ball mill: Grind the manganese ore …
Ball mill can grind ore to relatively fine and uniform particle size. The manganese ore of 0-12 mm is sent to the ball mill for grinding, and it can be ground into manganese powder of 0-1 mm. ... Reagents vary according to the type and grade of ore. Most manganese ore plants adopt an anionic reverse flotation process to obtain high-grade ...
1. Raw ore: rock manganese ore 2. Capacity: 10TPH 3. Feed size: <200mm 4. Output: 0-2mm 5. Location: South Africa
new manganese ore mines in future will thus be the sole responsibility of the State whereas processing ... erec-tion of mineral dressing plants in future manganese mines may also be the sole responsibility of the State. The production of manganese ores in India for the past five years is given in Table I. TABLE 1---PRODUCTION or MANGANESE ORE ...
manganese ore beneficiation plant china - africar-hire.co.za. Spotlight: Iron Ore and Manganese Ore Metallurgy 2011. and shape measurements applied to jig plant performance analysis ; author index The metallurgy of iron ore and manganese ore in South Africa is critical, Beneficiation covered DMS, gravity concentration, magnetic separation and flotation.
1 Main equipment of manganese ore process plant. The main manganese mining equipment is 2 sets of PE400 mm×600 mm jaw crusher, 2 sets of CXK1 600 mm×7 630 mm tank washing machine, 2 sets of ZD150 …
Manganese processing description from its geology mineral property to how to extract mineral from rock and placer deposit, related processing plant flow chart and layout design.
Manganese ore processing plant or manganese ore beneficiation plant consists of jaw crusher, hammer crusher, ball mill, classifier, flotation machine, concentrator, dryer mine feeder, hoist and conveyor.It has unique features such as high …
Manganese is considered a relatively rare metal as concentrations of it in ore of commercial importance are geographically limited. In nature, manganese is found in the form of oxides, carbonates, and silicates. Manganese ores are complex in the sense that they not only consist of a complex oxide mineral assemblage but these minerals are also very finely inter …
The commonly used beneficiation methods of manganese ore are gravity and magnetic separation, flotation, chemical beneficiation, etc. ... the grinding process adopts the rod grinding ball milling stage, and the equipment scale is φ 2100mm × 3000mm wet mill. ... By the early 1990s, there were more than 50 large and small electrolytic metal ...
Manganese is a type of common metal mineral in nature. More than 150 types of manganese minerals have been discovered so far, but only a small portion of manganese ore with mining and utilization value, mainly including pyrolusite, psilomelane, bog manganese ore, etc. Manganese has become an essential strategic mineral resource among countries and apply in …
Description: Manganese ore beneficiation plant can greatly upgrade manganese ores like manganese oxide ore, manganese carbonate ore, iron manganese ore, and polymetallic composite manganese ore. we will reply to you within 24 …
A manganese ore production line plays a crucial role in efficiently extracting and processing manganese, ensuring its availability for various industrial, technological, and environmental …
The ball mill is a well-known ore grinding machine and is widely used in mining, construction, and aggregate application. ... Ball Mill Liner: Natural rubber plate, manganese steel plate, ... and free operation training in mining, grinding, screening, crushing plant. Ball Mills Types.
The manganese ore is a rock type, has clay, a maximum input size of 100mm, manganese concentrate size is 0-25mm, the Mn grade in raw ore is around 18%, Fe2O3 accounts for 10% to 15%, SiO2 accounts for 25% to 35%.
The mill treats 550 tons daily of an ore carrying 13.25 oz. per ton silver, 0.071 oz. per ton gold, 0.5 per cent zinc, 0.5 per cent lead, and 2.0 per cent manganese. Primary crushing is carried out in two gyratory crushers making a …
All 5 / Chrome Ore 0 / Copper Ore Plant Case 0 / Gold Ore Plant Case 2 / Lead-zinc Ore Flotation Plant Cases 2 / Manganese Ore Case 1 / Tungsten/Tin/Ta&Nb Ore Beneficiation Plant 0 / Zircon Sand Case 0
The flowsheet of the Delta Manganese plant at Nelspruit is given in Fig. 1. The process consists essenti-ally of four main steps: (a) reduction of the ore from manganese (IV) to manganese (II) to solubilize it in sulphuric acid, (b) leaching of the reduced ore in spent electrolyte by the reverse-leaching technique to minimize the dissolution of ...
Screening equipment is used in a mineral processing plant to classify ore particles at different processing stages, ensuring that the size of the ore being handled is suitable for each stage, which improves processing efficiency and product quality. Vibrating screen: Separates ore by size using high-frequency vibrations. It is used for ...
Ball Mill; Wet Pan Mill; Raymond Mill; Spiral Classifier; Hydrocyclone; Gravity Separation. Shaking Table; ... Chrome Processing Plant; Manganese Ore Processing; Iron Ore Beneficiation Plant; Titanium Beneficiation Plant; ... Tin Ore Processing Plant; Lead Zinc Ore Processing; Chrome Washing Process; Contact Us +86-
The ball mill is a rotating cylindrical vessel with grinding media inside, which is responsible for breaking the ore particles. Grinding media play an important role in the comminution of mineral ores in these mills. This work reviews the application of balls in mineral processing as a function of the materials used to manufacture them and the mass loss, as …
حقوق النشر © 2024.Artom كل الحقوق محفوظة.خريطة الموقع