Hematite Gravity Beneficiation Production Line
The beneficiation process of hematite is closely related to the properties of hematite. Under normal circumstances, the beneficiation methods of hematite are mainly gravity beneficiation method, strong magnetic separation method, …
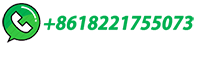