A practical guide to improving cement manufacturing …
The cement production process 1. The Quarry: The cement production process begins with the extraction of limestone and clay from the quarry. 2. Crusher and Pre-Blending: The material is then crushed to reduce particle sizes and blended to reduce variability in composition. 3. Raw Mill and Kiln: Raw materials and additives are
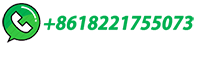