Cement Rotary Kiln Refractory Lining Selection Principles
Mini Cement Plant Hot Sale; Cement Plant 700 ~ 2000tpd; Cement Plant 2500~7000tpd; Cement Types Menu Toggle. OPC Manufacturing Plant; PPC Manufacturing Plant; ... There are many refractory materials that can be used to form the refractory lining of cement rotary kilns. For different parts of the rotary kiln, we may need to choose different ...
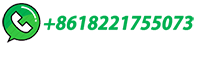