Working Principle of Crushers
Working Principle of Crushers. On left is a showing of the "standard gyratory with straight concaves" is a section through any vertical, radial plane in the crushing chamber of one of the intermediate sizes of the crusher. In order to understand the crushing action in such a chamber it is helpful to consider the process as though each step took place in an orderly, and …
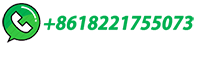