® Crushing Equipment |
For jaw crushers, we supply a range of jaw dies and liners with a variety of teeth options to best suit the application. ... All ® crushers are backed by our unrivalled Minerals service centre network that operates across more than 70 countries around the globe. This means that our experts are here to support you, every step of the ...
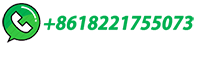