Nanoparticle preparation of pharmaceutical compounds via wet milling …
Wet ball media milled formulation using a non-toxic stabilizer (P188) exhibited favorable dimensional and aerodynamic parameters, ensuring effective delivery to deeper lung regions. ... The optimized wet milling process was found to be superior to precipitation based on assessments of physicochemical characteristics and aerosol performance. Wet ...
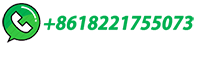