Utilization of waste heat from rotary kiln for burning …
The flue gases from rotary kilns reach different temperatures depending on the number grades air heater. Four-stage heater supplies gas temperatures of 300-380 ° C and 5 ÷ 6-stage 200-300 °C. The hot air discharged from ... The possibilities of waste heat …
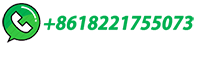