Superior™ MKIII Series primary gyratory crushers
Superior™ MKIII primary gyratory crushers bring safety and easy maintenance to any crushing plant. Hydraulic separation and individual lifting of shells creates a better environment for any workers on site working with the equipment. The SmartStation also improves operational safety.
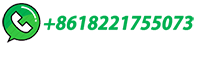