Explain in detail the process and configuration of the sand
Mohs hardness: around 7. Material advantages: Hard quality, strong pressure resistance, is the main material for the production of artificial sand and gravel.
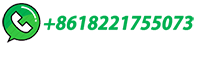
Mohs hardness: around 7. Material advantages: Hard quality, strong pressure resistance, is the main material for the production of artificial sand and gravel.
How you select your primary crusher will be based on factors like moisture content, maximum rock lump size, material density SG, abrasion index, degradability and it being prone to dusting or not. The crusher capacities given by manufacturers are typically in tons of 2,000 lbs. and are based on crushing limestone weighing loose about 2,700 lbs. per yard3 and …
Rock hardness refers to the resistance of a rock to scratching. Its value equals the uniaxial compressive strength (MPa) of the rock divided by 10. Rock hardness and compressive strength have a certain connection, but also have big differences. Rock hardness is the resistance of a part of the rock surface when it is pressed into another object.
Primary crushing operations takes boulder size feeds (20 to 100 inches) and reduces the material to secondary crusher feed size (1 to 20 inches) or mill feed size (0.5 to 3 inches). This video illustrates single- and double-toggle jaw crushers. ... material, and hardness must be considered. Output size ranges. Crushers accept dry or wet input ...
A gyratory crusher is an ore processing machine that crushes the ore between an eccentrically mounted cone and a crushing throat that is fixed. In mining, the most important criteria for effective crushing of oresis to choose the type of crusher that …
Hard materials causing severe abrasive wear are reduced with slow running machines such as jaw crushers and gyratory crushers, which function by developing mainly a compressive …
Rockwell hardness test is a fast testing method found for production control, with direct reading, used primarily for metallic materials. Rockwell hardness (HR) is calculated by measuring the depth of the indentation after inserting the indenter into the sample material at a given load, which reflects the measured resistance of the metal to indentation.
Unlike traditional mechanical systems, these crushers use hydraulic cylinders to adjust the crusher's setting and to provide overload protection. The hydraulic system allows for precise control over the jaw movement, enabling …
The choice of cone crusher will depend on the specific requirements of the application, including the type of material being crushed, the desired product size, and the production capacity required. By understanding the different types of cone crushers available, you can make an informed decision when selecting the right cone crusher for your ...
Consider factors such as material type, size, and hardness when selecting a crusher. With the right crusher, you can improve your processing efficiency and reduce downtime, ultimately saving you time and money in the …
For example, when processing limestone, a cone crusher can turn limestone with a Mohs hardness of about 3 into gravel sizes. For harder basalt, with a Mohs hardness of around 5-6, it can make the pieces even smaller. …
As a secondary crusher, HSI crusher can process material with a little hardness and abrasive. It is sometimes be used in primary crushing process, but only can process soft material like limestone, gypsum. Cone crusher looks like gyratory crusher but without a steep crushing chamber.
Crushing is the reduction of large material into smaller sizes. It is often one of the first steps in any aggregate or mineral processing plant and is accomplished with various types of crushing equipment. These machines …
Various types of crusher and mineral separator may be employed depending upon the throughput, hardness, and properties of the ore being processed. In all cases, the crushing stage is essentially achieved by transferring a mechanically amplified force (via mechanical advantage ) to a material, to breakdown the bonds which hold the material together.
Such a variation would explain the discrepancy in the computer model. Hardness tests performed in this study reveal that this is not the case. ... It has been assumed that there is a variation in obtained hardness in a worn crusher liner; that higher crushing pressure would yield higher hardness, and consequently a lower wear rate in relation ...
Hardness tests. In order to improve the design of crusher liners, hardness tests have been used in the mining and aggregate industries. This research involved a computer model that can predict the geometry of a worn …
In the mining, construction and material processing industries, crushers play a vital role. Among them, jaw crusher and hammer crusher are the two most common and important crushing equipment. Although they are both used for material crushing, they have significant differences in application scope, working principle and effect.
Depending on the hardness and size of the feed, coarse impact crushers reduce the material to a product size 150 and 200 mm and attain reduction ratios material to a product size between 6:1 and 20:1. ... Crusher type Particle size and shape . Jaw Few fines. Tendency to agglomerate the particles . Cones Few fines. Particles with cubical shape ...
During the working process of jaw crusher, the material is in direct contact with the jaw plates, and the jaw plates bear huge crushing force, especially for some materials with higher hardness. The strong force will cause the installation bolts of the jaw plates to be vibrated and loosen, thereby aggravating the wear of the jaw plates, or even ...
What is a primary crusher? A primary crusher is a machine used to perform preliminary, rough crushing of large pieces of hard materials such as rocks, ores, concrete, …
Table Source: Wikipedia (Crushers) Cone crushers use a spinning cone that gyrates in the bowl in an eccentric motion to crush the rock between the cone surface, referred to as the mantle, and the crusher bowl liner.Gyratory crushers are very similar to cone crushers, but have a steeper cone slope and a concave bowl surface. As the gap between the bowl liner …
What is a crusher? A crusher is a machine that is designed to reduce large rocks into smaller rocks, gravel, or rock dust. Crushers may be used to reduce the size of materials, or change the form of waste materials so they can be more easily disposed of or recycled, or to reduce the size of a solid mix of raw materials so that pieces of different composition can be …
Cone crusher is a type of crushing equipment whose crushing cone rotates in the conical cavity within the shell to realize intermediate crushing or fine crushing of material through squeezing, bending, shearing, and impacting. At the end of the nineteenth century, the Simons brothers of the USA invented this equipment based on gyracone crusher ...
There are two critical factors influencing choice of crushing techniques and equipment. Hardness of the rock and abrasiveness. Hardness of the rock is typically measured using the Mohs scale, where talc is rated as 1 (softest) and diamond as 10 (hardest). This scale helps determine what type of rock crusher is needed for the job.
Compressive crushers that press the material until it breaks, and impact crushers that use the principle of quick impacts to crush the material. Jaw crushers, gyratory crushers and cone crushers operate according to the …
The cone crusher is one of the most popular and commonly used crushing equipment in quarries, mines, and other industries. It is designed to crush materials with high hardness and medium hardness, such as basalt, granite, limestone, gravel, quartz, iron ore, copper ore, and so on.
This paper presents the characterization of a secondary cone crusher concave liner made of Hadfield steel used in Chilean mining after crushing copper minerals during all service life.
In a stationary jaw crusher, jaw plates are typically set low enough to let the jaw move at a slow, steady pace. In a jaw crusher with movable jaw plates, on the other hand, jaw plates will move much faster to break up large rocks into …
This is a type of crusher that is widely used in the primary and secondary crushing processes. ... This angle depends on the size, hardness and frangibility of the material. It cannot be selected as too large or too small. The nip angle in primary is lower than in secondary .
In this Cone Crusher article we want to educate you about what to consider when purchasing a cone crusher. It also will inform and educate you if you are a current owner or operator of a Cone Crusher. If you have a good base of knowledge about cone crushers you can skip through the article by choosing the topics below.We will be exploring in more detail the following:Cone …
حقوق النشر © 2024.Artom كل الحقوق محفوظة.خريطة الموقع