(PDF) Flotation of Iron Ores: A Review
The aim of this paper is to provide a well-detailed, well-referenced source for the current status of iron ore flotation, and thus provide a useful guide to its future development and to further ...
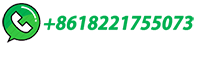
The aim of this paper is to provide a well-detailed, well-referenced source for the current status of iron ore flotation, and thus provide a useful guide to its future development and to further ...
Prasad et al. (1988) have studied iron ore slimes processed by magnetic separation at the Kiriburu mines in India. A c oncentrate containing 63% Fe and 3.3% Al 2 O 3 with an iron recovery of
Magnetic separation is the most commonly used beneficiation method for ferrous metal ore such as iron ore. It is divided into weak magnetic separation and strong magnetic separation according to the different magnetic …
Gravity separation has also been used in combination with flotation at many REE processing operations throughout China [25, 93]. The froth flotation process has been used on Pea Ridge iron ore's tailings to concentrate the REEs . Yang et al. studied the beneficiation of vein-type apatite REE ore from Mongolia.
Common techniques include magnetic separation, flotation, and gravity separation. 4. Thickening and Filtration: The slurry from the beneficiation process is thickened and filtered to remove excess water, ... It commands a higher price and is in demand for producing high-quality steel products. Iron ore fines, although having lower iron content ...
In this study, a process of magnetizing roasting followed by low-intensity magnetic separation (MR-LMS), which is used to separate and recover iron from a low-grade carbonate-bearing iron ore ...
In this study, an approach of producing high-purity iron is proposed via a direct reduction of iron ore–melting separation–refining process, by which high-purity iron with purity up to 99.987% …
An economic analysis shows a significant annual revenue of 14,333.52 thousand USD based on high-purity (>99.5%) SO 2 and NO 2 products recovered from a typical scale (~1000,000 m 3 /h) of iron-ore sintering flue gas, not only offsetting the total operating cost of the entire adsorption capture-distillation recovery process but also generating ...
The chemical multi-element analysis of raw ore, transformed products, iron concentrate, and tailings is shown in Table 2. Table 2 shows that the TFe content in the raw ore was 48.15 %, and the FeO content was less than 0.01 %. This indicated that iron in the raw ore was not present in FeO, indicating a very low content of highly magnetic magnetite.
Sieving is a process of separation of the ore material into multiple grades by particle size [1]. The screen is a vibrating mining machine, that is driven to motion by a rotating of unbalanced ...
Product analysis shows that after SMR, iron minerals such as siderite and hematite transform into magnetite, with a substantial increase in magnetism, which is conducive to the separation...
Its advantages over precipitation enable the wide application of the extraction method, which has been a research hotspot in the world in petrochemistry, hydrometallurgy, fine chemical industry, separation, and purification of biochemical substances.Iron extraction has been studied extensively due to the damage caused by iron ions to water, soil, and organisms.
Some possible applications for iron ore tailings (IOT) after the separation step. Model houses built using IOT in collaboration projects of UFMG with the mining companies Samarco and Gerdau. 93,94 +5
ST Equipment & Technology (STET) has developed a dry separation system using a tribo-electrostatic belt separator. This technology does not require water or chemical additives. …
Traditional methods of iron ore separation treatment include gravity separation, roasting, magnetic separation, leaching, and so on [8, 9, 10, 11]. Gravity separation …
Boron is an important industrial raw material often sourced from minerals containing different compounds that cocrystallize, which makes it difficult to separate the mineral phases through conventional beneficiation. This study proposed a new treatment called flash reduction-melting separation (FRMS) for boron-bearing iron concentrates. In this method, the …
Subsequent magnetic separation tests were further conducted on the reduction products. A reduced iron powder with a Fe grade of 85.67 per cent was obtained at a Fe recovery of 87.82 per cent under optimum reduction conditions where a metallisation rate of 85.82 per cent was achieved. ... Upgrading an Australian iron ore by reduction and ...
Skarn deposits, among the world's most abundant and economically significant ore types, are categorized into seven main groups based on key metals: Fe, Au, Cu, Zn, W, Mo, and Sn skarns (Einaudi et al., 1981, Meinert et al., 2005).They are also important types of deposit for high-grade iron and copper (Li et al., 2019a).Especially in China, iron and copper skarn …
Major impurity elements in iron ore are silicon, aluminum, phosphorus, and sulfur. Often, a chemical separation is the only method able to remove phosphorus from iron ores.
In iron ore processing plants, different tailing streams are usually transferred to the tailings thickener for partial dewatering and finally transferred to the tailings dam as a single stream. Therefore, the mixing of different tailings streams happens. This way can challenge the process of reprocessing the tailings in the tailings dam since the mixing of different tailings …
The chemical and physical properties of iron ore tailings are comprehensively examined in this review, and various beneficiation and metallurgical recovery techniques such …
The reverse cationic flotation route widely used in the iron ore industry is less selective for alumina–hematite separation than for quartz–hematite separation. Pradip et al. (1993) studied the flotation of an alumina-rich Indian iron ore and reported that only 60% of the iron could be recovered in reducing the aluminum content from 11.6% ...
recovery and separation of iron from iron ore using innovative fluidized magnetization roasting and magnetic separation j. yu, y. han*, y. li, p. gao
Iron ore separation process. Separation is the most technically demanding part of the ore separation process. There are mainly gravity separation, magnetic separation, flotation and other separation methods. ... Hongji products have won the favor of more than 130 countries with their high quality and perfect after-sales service. Become the ...
What is bauxite used for? Bauxite ore is the world's primary source of aluminum production. With aluminum appearing in products ranging from airplane parts to beverage cans, many manufacturing markets need a steady source of this metal. Bauxite ore can deliver on these needs. It is also a key component of cement, food additives, and glass.
Today, I will share with you the magnetic separation process of iron ore. Magnetic Separation Principle. Magnetic separation is a beneficiation method that uses the magnetic difference between minerals in a non-uniform magnetic field to separate different minerals. Magnetic separation is the most commonly used beneficiation method for ferrous ...
This chapter reviews current iron ore comminution and classification technologies and presents some examples of flowsheets from existing operations. ... before secondary crushing, primary screens, and product screens for lumps and fines separation. Ore grade is determined from the blasthole drill cuttings in the mine and sample cutters in the ...
Zhong et al. performed a pilot test of the coal-based direct reduction of a low-grade iron ore and obtained iron ore powder with the total iron recovery of 85.61% after the magnetic separation of the direct reduction products (Zhong et al., 2020). In the low-grade direct reduction test, high iron recovery rate is typically obtained, and the ...
Turning to iron ore exports and imports, the tonnages are summarized in Table 1.1 for 2012 and 2018 (Australian Department of Industry, Science, Energy and Resources, 2021; US Geological Survey, 2020; United National Conference on Trade and Development (UNCTAD), 2021).As shown in Fig. 1.3, China is the largest iron ore importing country and imported about …
The ore is mainly composed of magnetite, hematite, martite, and quartz. It is very difficult to produce a high-quality iron ore concentrate by magnetic separation alone for this type of iron ore. The ore is first ground using ball mills down to about 90% -75 μm.
حقوق النشر © 2024.Artom كل الحقوق محفوظة.خريطة الموقع