Copper Smelting Process
There are several methods of copper smelting, the popular ones being reverberatory smelting and oxygen flash smelting. Both methods require the resultant molten copper to be further processed to achieve a grade of 99.9% …
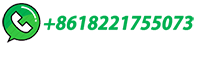
There are several methods of copper smelting, the popular ones being reverberatory smelting and oxygen flash smelting. Both methods require the resultant molten copper to be further processed to achieve a grade of 99.9% …
Copper processing - Ores, Refining, Smelting: Principal forms in which copper ores are found include native copper, porphyry copper, massive deposits, and mixed ores. Native copper is simply the metal found unadulterated in nature. Occasionally copper is still found in its native form, but more frequently it is mixed with other minerals, some of which may have value …
Smelting, leaching, and electrolysis are used to extract copper from these ores and minerals. Chile, Peru, and China are the three biggest copper-producing countries. It is found in both its native and combined states. The …
Process Flow. In copper matte smelting, fine and pulverized burdens (concentrate, solvent, dust, etc.) are uniformly mixed, dried (moisture less than 0.3%), and then stored in the feed bin at the top of a furnace. ... The copper production capacity of 1 flash furnace of the Saganoseki Smelter in Japan reached 450 KTA in 2000. The daily feed ...
baiyin furnace increases copper production capac-ity to 100,000 tons per year. The furnace'sservice life is extended to 24 months, and the production environment is improved. Technical Process Initially, the baiyin copper smelting process was air smelting. In 1988, oxygen-enriched air smelting was adopted, and the oxygen concentra-tion was 45 ...
Processing of Copper Ore. The first step in processing the ore removed from the mine is to break the large rocks of ore into smaller pieces. This is accomplished by a variety of subsequent …
Copper processing is a complicated process that begins with mining of the ore (less than 1% copper) and ends with sheets of 99.99% pure copper called cathodes, which will ultimately be made into products for everyday use.
In this study, the thermodynamic simulation model and system of the copper side-blown smelting process were established using the chemical equilibrium constant method, based on the process reaction mechanism, multiphase equilibrium principle, and MetCal software platform (MetCal v7.81). Under typical production conditions, the composition of the product …
smelting was developed. Newer processes are the Isasmelt/Ausmelt/Csiromelt (furnace with vertical blowing lance), the Noranda and CMT/Teniente reactors (developed from converters), …
Process control in flash smelting is based on mass and energy balance from which the operational parameters (oxygen coefficient, oxygen enrichment, and flux demand) are obtained to achieve matte and slag with defined compositions and at defined temperatures. Mineral compositions of copper concentrates, and their blends, have been used in order to optimize …
Throughout this century the major production of copper (as it relates to Copper Smelting) and most other nonferrous metals has been through pyrometallurgical. ... Copper Smelting Process. In the autogenous system …
The copper concentrates are fed through the flash smelting furnace with oxygen-enriched air. In the furnace, the concentrates are instantly oxidized, after which they melt and separate by their own reaction heat into copper matte with a grade of 65% and slag consisting of iron oxide, silica, and other compounds. Reaction in the flash smelting ...
In a flash-smelting process for the production of copper mattes and copper, the description of the particle heat-up to the molten state is of great importance [44]. As chalcopyrite melts around 1150 K [45], the kinetic data presented …
At this plant near Bingham Canyon, Utah, copper concentrate is turned into metal in a process called smelting. Smelting heats up the concentrate at very high temperatures and removes most impurity elements. Subsequently, iron and sulfur are removed in the …
Bottom-blowing copper smelting technology was initiated and developed in China in the 1990s. Injection of oxygen-enriched high-pressure gas strongly stirs the molten bath consisting of matte and slag. Rapid reaction at relatively lower temperatures and good adaptability of the feed materials are the main advantages of this technology. Development and …
The effectivity of present copper smelting technologies have their roots in industrial and laboratory-scale experience accumulated over the past decades. ... Wang L, Yang C. 2007. Intelligent prediction model of matte grade in copper flash smelting process. Trans Nonferrous Met Soc China. 17: ... Optimal production of electrolytic copper ...
Mitsubishi copper smelting, Vanyukov copper smelting, ISA process, Ausmelt process, and oxygen-rich bottom blowing smelting are also extensively used. Application of oxygen is a great advancement of matte-making smelting technology. The oxygen-enriched concentration in various matte-making smelting processes is from 40% to technical pure oxygen.
A schematic diagram of the conventional process for the production of copper and the SX/EW process can be seen here. Conventional Copper Extraction . Conventionally, copper is recovered by a pyrometallurgical process known as smelting. In this process copper ore is mined, crushed, ground, concentrated, smelted and refined.
In a flash-smelting process for the production of copper mattes and copper, the description of the particle heat-up to the molten state is of great importance [43]. As chalcopyrite melts around 1150 K [44], the kinetic data presented …
Copper production is complex and multi-stage: it involves mining, crushing, milling, ore concentration, smelting, refining and waste management. The metal ore mining industry, including copper, generates over 10 billion tonnes of slags, dusts and aerosols as by-products, which are contaminated with metals and metalloids, including toxic ones ...
After pyrometallurgical smelting (or a multi-step recycling process) and a downstream electrolytic refining process, the copper is ready for further use in its purest form, as a high-quality cathode. These cathodes, which have a copper content of more than 99.99 %, are first melted down in a carefully monitored process and then cast ...
The smelter is basically a large furnace which melts the concentrate and drives off the sulfide to leave molten copper metal this is still contains impurities and it needs to be refined further to make it a salable product. Returning to the overall process; that is the process for the sulfide ores and the oxide ore as I said are treated ...
• Material Production: Smelting is integral to the production of a wide range of materials used in construction, transportation, electronics, and countless other ... Copper Smelting: To produce bronze, people became adept at smelting copper ores, a process that involves heating copper-rich minerals to high temperatures. Early smelting ...
The Process. The concentrated ore is heated strongly with silicon dioxide (silica) and air or oxygen in a furnace or series of furnaces. ... The end product of this is called blister copper - a porous brittle form of copper, about 98 - 99.5% pure. Exploring the redox processes in …
Occasionally adopted in preference to smelting (or pyrometallurgy, as it is generally known), leaching, or hydrometallurgy, is carried out at lower temperatures and thus eliminates the generation of sulfur …
The oxygen bottom blown copper smelting process is a newly developed intensifying smelting process, which has been widely applied to the copper productions in China in the past 10 years [6, 23].This process was industrially tested initially in the Shuikoushan (SKS) smelter in 1990 and was named originally as "SKS process ", which is also called BBS (bottom …
a new smelting facility or modernizing an existing operation. Recent developments in copper smelting are reviewed with particular reference to the newer smelting processes. Cri teria for process selection, the impact of oxygen enrichment, energy consumption, environmental controls, and investment costs are discussed. INTRODUCTION
What is copper smelting? The method of extracting pure elemental copper (Cu) from copper concentrate (CuFeS 2).
The copper smelting industry is an important part of the traditional non-ferrous industry, as well as a basic component of the emerging communication and new energy industry (Dong et al., 2020).In the past 10 years, global primary copper smelter production has increased by more than 40% and showed an accelerated growth trend (International Copper Study …
The production of copper in the flash smelting process is accompanied with a large amount of copper-rich slag, which has to be treated with the aim of copper recovery. Copper flash smelting consists of blowing fine, dried copper sulphide concentrate and silica flux with air, oxygen-enriched air or oxygen blast into a hot (≈1500K) hearth-type ...
حقوق النشر © 2024.Artom كل الحقوق محفوظة.خريطة الموقع