(PDF) Antimony Production and Commodites
The process presented is appropriate for antimony extraction with significant benefits associated with an increased value of galena concentrate and its own market value.
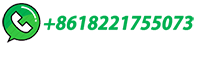
The process presented is appropriate for antimony extraction with significant benefits associated with an increased value of galena concentrate and its own market value.
sheets of 99.9% purity. INTRODUCTION Primary lead production is usually ... antimony, tin, bismuth, selenium, tellurium, silver, and gold, as well as ... refined the process for direct refining of bullion and the modified process is trademarked LEADBOR). Applied to granulated bullion, Fluobor is an ...
USAC operates the only significant antimony smelter in the United States and it is in a "sold out" condition. The Company has proven experience in underground and open pit mining, flotation and gravimetric milling, crushing and screening, dry grinding, cyanide leaching, precious metal refining, pyro-metallurgy, and marketing.
Refining techniques are employed to further purify and process antimony after it has been extracted from its ore. These techniques aim to remove impurities and obtain high-purity antimony products suitable for specific …
Pyrometallurgy has been the main process of antimony extraction ... Blister copper in turn is refined in an anode furnace (fire refining), to generate copper anodes with >99 (weight) ...
The main purpose of this study was to separate lead from crude antimony through an oxidation pyro-refining process and by using sodium metaphosphate as a lead elimination reagent. The process parameters that will affect the refining results were optimized experimentally under controlled conditions, such as the sodium metaphosphate charging dosage, the refining …
The total removal ratio of impurities through the two-step process can reach 99.524 %, and the antimony trisulfide product with a purity of about 99.99 wt% can be obtained …
Computation-assisted analyzing and forecasting on impurities removal behavior during zone refining of antimony. ... Sb with a purity level of 4 N (i.e. 99.99%) is an important ingredient in Bi 2 Te 3-type alloys utilized in ... When aiming to introduce a zone refining process in the shortest possible time, a combination of different situations ...
The oxide volatilization process to recover additional antimony usually treats the residue, containing 12–30% antimony. The liquated product, called crude, liquated or needle …
Antimony and bismuth are two of the most problematic impurities in copper electrorefining. As a result, much research has been done investigating the ways to remove them. Processes that are currently being used industrially include anode additions, liberators, ion exchange (IX), and solvent extraction (SX). Of these, liberators and anode additions are the …
Under these conditions, the antimony content in the oxidized solution is reduced to 0.092 g/L, and the antimony precipitation ratio is over 99.80%. Compared with the traditional air oxidation process (Yang et al., 2002), this antimony precipitation process is improved significantly.
In this work, a two-step vacuum metallurgy method was proposed to produce Sb2S3 from complex lead-antimony sulfide ore. As revealed from the experimental results, jamesonite (Pb4FeSb6S14) is ...
Antimony is one of China's four strategic resources, mainly used in flame retardant, alloy, medicine, electronic materials and other fields (Yang and Wu, 2014; Guo et al., 2017).The United States Geological Survey (USGS) shows the world antimony output will reach 110,000 tonnes, of which China will account for 60,000 tonnes in 2022 and be 55% of global …
Results of electrolysis of antimony (99.56% Sb) in a sulfate-fluoride electrolyte are provided. Electrolysis parameters and distribution of 20 associated elements between the cathode metal, sludge ...
The compounds float upward with the sawdust and become slag, so as to remove the arsenic and antimony. Besides, China has developed the pyrometallurgical refining process dominated by vacuum distillation, which has increased refining efficiency and reduced environmental pollution.
lighted antimony in its critical raw materials report, as the element with the largest expected supply–demand gap over the period 2015–2020. This has sparked efforts to find secondary sources of antimony either through the recycling of end-of-life products or by recovering antimony from industrial process residues. Valuable residues are ...
Spent lead–acid batteries have become the primary raw material for global lead production. In the current lead refining process, the tin oxidizes to slag, making its recovery problematic and expensive. This paper aims to present an innovative method for the fire refining of lead, which enables the retention of tin contained in lead from recycled lead–acid batteries. …
The FCC unit is regarded as the most important conversion unit and the cash cow of the refinery because the fuel produced from this unit alone accounts for 35 to 50% of the total gasoline produced globally in the petroleum industry [3], [4], [5], [6].However, the world crude oil supply changes towards heavier crudes, coupled with the quest by refiners to process cheaper …
An electrolytic refining process is used in order to obtain antimony with an overall impurity content not above 0.1–0.3%. In this this case the complete scheme for comprehensive treatment of antimony raw material includes: flame refining of ferrous metal electrolysis in solutions, solution purification from accumulated impurities, and anode sludge treatment with …
Noble antimony is the carrier of precious metals in the antimony smelting system and has a very high added value. This study proposes a novel, green, and effective vacuum gasification process for purifying antimony and recovering precious metals from noble antimony. Saturated vapor pressure and separation coefficients (β) were used to qualitatively analyze …
They proposed a pyrometallurgical process based on reduction smelting, alkaline refining, and oxidation to extract antimony from antimony dust and produce Sb 2 O 3 with a purity above 99.8 % [76 ...
Ultra-high purity antimony (Sb, 99.999%) has a wide range of applications especially in semiconductors, either as tuning element or as main component in specific compounds such as InSb, GaSb and SbTe. ... Method for removal of lead and arsenic in crude antimony vacuum refining process. CN104328289A (2014) Google Scholar [10] Y. Dai, B. …
When classifying impurities in commercial pure antimony (Sb, 99.8%), arsenic (As) and lead (Pb) should be brought to the forefront consideration. Due to the known difficulty of …
Lead bullion contains many other metallic impurities including antimony, ... copper, tin and zinc. Refining Process of Lead in Detail: a. Removal of Copper Copper is the first of the impurities to be removed. The lead bullion is melted at about 300–600 °C and held just above its ... either soft Lead with 99.97% purity or hard Lead of varying ...
Most commercial grades of antimony xide contain between 99. 2% and 99.5% antimony . ... are also used in decolorizing and refining ... The process presented is appropriate for antimony ...
Current extractive metallurgy techniques for lead refining by the Betts Electrorefining Process (BEP) are reviewed. In the BEP, refined lead (>99.99%) can be produced by the electrorefining of impure lead anodes. The process relies on the selective dissolution of lead which leaves behind a strong and adherent layer of solids (slimes) containing the noble …
Introduction to the pyrometallurgical refining process of crude lead 1 Copper removal process This process is based on the principle that the affinity between copper and sulfur is ...
An improved process for refining lead bullion containing antimony, in which the bullion is initially heated in a refining vessel to about 25° F. (14° C.) above the bullion melting point, and is thereafter kept molten primarily by exothermic process reactions. The process includes the steps of melting the lead-antimony bullion, agitating the bullion, adding caustic soda and metallic …
In the process of refining with the reagents, the reactions occur with the evolution of H2O during the decomposition of phosphoric acids (for example, H 3PO → HPO + H2O), phosphoric salts …
antimony sulfide concentrates to obtain metallic antimony and antimony xide are discussed, and methods of refining antimony from impurities are also analyzed. Keywords: antimony, compounds, minerals, raw materials, alloys. Received 01 September 2022 Accepted 18 November 2022 Journal of Chemical Technology and Metallurgy, 58, 5, 2023, 988-998
حقوق النشر © 2024.Artom كل الحقوق محفوظة.خريطة الموقع