Hard Rock Mining Equipment | Crushing Plants
DOVE is the world's major manufacturer of an unmatched range of Semi-stationary Hard Rock mining equipment and crushing plants, for gold, platinum metals, base metals, and ferrous metals, producing high quality Ball Mills, Jaw …
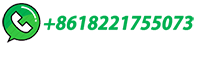