Iron Ore Agglomeration Technologies
The formation of liquid phases, which agglomerate the iron ore, in pellets is achieved by an external source of energy (fuel, natural gas or pulverized coal), ... Review of organic binders for iron ore concentrate agglomeration. Minerals and Metallurgical Processing. 2014; 31 (2):72-94; 13.
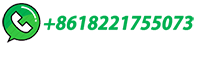