(PDF) Leaching of gold ores with high cyanicides: a
The aim of the work is the flotation processing of gold-containing tailings using composite flotation (CF) agents. According to the results of chemical analysis, the studied tailings sample ...
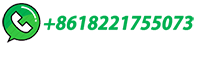
The aim of the work is the flotation processing of gold-containing tailings using composite flotation (CF) agents. According to the results of chemical analysis, the studied tailings sample ...
The goal in mineral processing is to produce maximum value from a given raw material. This goal can be a crushed product with certain size and shape or maximum recovery of metals out of a complex ore.
silver processing, preparation of the ore for use in various products.. Silver has long been valued for its white metallic lustre, its ability to be readily worked, and its resistance to the corrosive effects of moisture and oxygen.The lustre of the pure metal is due to its electron configuration, which results in its reflecting all electromagnetic radiation of wavelengths longer than 3000 ...
In another test with high grade chromite ore, sustainable product qualities were achieved up to a recovery of 93.22% in comparison with the 66.08% achieved with a conventional shaking table, within and approx. 47–48% final grade level. Additionally, product grades and recoveries up to 50.20%–58.36% with deslimed −400 µm low grade ...
It had been reported by the management that BGM grinding circuit was designed to produce final product size of 125 μm, which had not been achieved for a long period of time under both, low to ...
extraction of gold from these ores is of particular impor-tance for all gold-mining and processing countries in the world [3], since the reserves of placer gold are depleted, oxidized ore is easily processed and the strategic needs to increase the size of difficult-to-process ores, while it should be kept in that reserves of these ores make up ...
Plant, the r.o.m. of -8" size is crushed. The final product from crushing plant, i.e. -10 mm size is stored in a 1,500 tonnes capacity fine ore bin for subsequent treatment, i.e., grinding. The Milling/Grinding process of gold ore employs two distinct grinding techniques. The first technique involves grinding
In the gold mining industry, smelting is the final stage of extracting pure gold from ore. This process involves melting the gold-laden material to separate the precious metal from impurities. Here, we'll delve into the two primary methods used to smelt gold-loaded carbon from cyanide leaching plants: desorption electrolysis and direct smelting. Desorption Electrolysis […]
The goal is to get the ore just the right size so we can get as much valuable stuff out of it as possible. The grinding process helps separate the good minerals from the useless parts and makes sure the next steps, like …
3 2.0 Major Processes of Mineral processing: The following are the major processing methods involved in ore dressing/ mineral processing: 1. Size reduction (Crushing,Grinding ) 2.
This paper describes the metallurgical processes at the 80 000tpd Ok Tedi Mining Limited concentrator, which treats copper- gold ore by single-stage crushing, SAG and ball milling and flotation to produce over 500 000tpa of concentrate. Plant and process developments, including installation of column cells, reduction of fluorine in concentrate, use of sulphidisation and …
In Grinding, selecting (calculate) the correct or optimum ball size that allows for the best and optimum/ideal or target grind size to be achieved by your ball mill is an important thing for a Mineral Processing Engineer AKA Metallurgist to do. Often, the ball used in ball mills is oversize "just in case". Well, this safety factor can cost you much in recovery and/or mill liner …
Gold-containing ore processing technology has been developed by using chemical, X-ray phase, mineralogical, X-ray fluorescence analyses. ... The particle size of Au in the product varies from 0.5 to 18.8 μm. 77.12% of gold is recovered from concentrate of 10 μm by direct cyanidation. "Sulfanol" was used to recover 83.71% of gold.
Comminution is the process of reducing the particle size of an ore to liberate the ore minerals from the gangue minerals. Thus, comminution strongly controls the overall efficiency of a mineral processing operation. Even though blasting as the first step of extracting an ore from the ground is also a form of comminution, the focus here
(KHD HPGR) is advocating this new circuit and has reported on recent project studies, and a few operations (iron ore and limestone processing), with final product sizes of 75 μm or as low as 15 μm, are feasible and enable significant energy reduction (more than 50% overall if compared to traditional circuits with tumbling mills).
The gold extraction method mainly depends on the chemical composition of the gold ore, the mineral composition, the gold particle size of the gold, and the requirements of the finished product. Gravity separation, flotation, magnetic separation, cyanidation, these different extraction methods can maximize gold recovery.
Iron oxide copper gold ore refers to the symbiosis of copper ore and gold ore in gold ore in some form. Its amount is about 10 million to 4 billion tons. IOCG ore contains copper with a grade of 0.2% to 5% and gold with a content of 0.1 to 1.41 grams per ton.
The main process of the CIP gold processing plant to extract gold from ore and convert it into pure metal can be divided into 6 steps: crushing, screening, grinding, classification, carbon slurry gold extraction and tailings …
The methods of extracting gold from quartz vein ore, sulfide ore, polymetallic gold-bearing ore, gravity separation, flotation, and cyanidation can all achieve high recovery rates.
The design of ore processing plants is influenced by a multitude of factors that collectively shape the overall efficiency, cost-effectiveness, and environmental sustainability of the operation. First and foremost, the type and characteristics of the ore being processed play a pivotal role. Whether it's copper, gold, iron ore, or any other mineral, the ore's physical and …
The level of comminution required for the low-grade hematite ore is similar to high-grade ores to deliver products of the same size specifications, lump and fines. ... moisture control in processing facilities and of final products has also addressed changes to material types and blending techniques. ... globally this technology is used in ...
Considering the different gold minerals present alone or combined with the host rock, it will be necessary to discharge the unwanted material in order to increase the concentration of gold in an economically manner. This part treats the strategy of beneficiation as a combination of several …
The Mineral Processing Flowsheets shown on the following pages are based on actual data obtained from successful operating plants. Metallurgical data are shown in these flowsheets which incorporate Crushers, Grinding Mills, Flotation Machines, Unit Flotation Cells, and Selective Mineral Jigs as well as other standard milling equipment. The Flotation Machine, …
Today, Outotec can offer processes and equipment that cover the full gold value stream from ore to dore. This includes all three main oxidative processes for the treatment of refractory gold concentrates – BIOX, …
Based on the expansion of the existing mineral processing workshop, the mineral processing scale reaches 6000 tons/day, and the final mineral processing product is gold concentrate. Xincheng Gold Ore, belonging to Shandong Gold Mining Co., Ltd., Shandong, China, is a large, national gold production enterprise with a comprehensive production ...
A case study was undertaken at a gold mine in the Free State on the influence of the fragment size distribution on 'free gold', the effect of ore loss and dilution on the mill efficiency, and time tracking of ore movement from source to the plant. ... the ore passes through before the final product is extracted. The ore flow sheet guided the ...
where R represents the ratio: % Pb in crude ore/% Cu in crude ore Formula (32) is very convenient for milling calculations on ores of this type. Example: An ore contains 5% lead and 1% copper. The ratio of perfect concentration for a concentrate of maximum grade and recoveries of lead and copper would be:
Oxidized gold ores are relatively easier to treat using cyanide leaching than the sulfide ores because the oxidation process reduces the size of the sulfide matrix and liberates the gold particles. In addition to cyanide leaching, oxidized gold ores can also be treated using gravity separation methods, view Comprehensive Overview of Gravity ...
According to the particle size characteristics of the raw ore, the separation operation can adopt wet screening or hydraulic classification, or both. ... The lump ore can be used as the final product. When processing clay, wash the clay to disperse the mixed materials (gravel, mica, etc.), then separate, concentrate, and filter to obtain high ...
High product quality and high concentrate grade: After refined processing and extraction, the final gold product is of high quality and high concentrate grade, which can meet various application …
حقوق النشر © 2024.Artom كل الحقوق محفوظة.خريطة الموقع