Wet High Intensity Magnetic Separation
WHIM is the short acronym for Wet High Intensity Magnetic Separation. ... However, processing of reduction-roasted ore in a conventional taconite plant would require some modifications, because artificial magnetite has a higher remanence and coercivity than natural magnetite. ... Highly metamorphosed schistose iron ore from the Marquette range ...
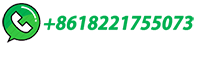