Iron ore
Iron ore is integral to the steel-making process and one of the most sought after commodities in the world. Contact us; English. ES | Español | Chinese. ... The crushed ore is sorted over screens and resized to different specifications, such as lump and fines products. Once the iron ore is processed, a stacker builds a stockpile in the ...
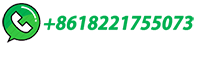