Steel Balls Consumption & Ball Mill Effect
6. Control the speed of the ball mill. Under the condition that the steel balls of the ball mill are configured and practical, the rotating speed of the ball mill increases, and the steel balls of the cylindrical bearings will drop into piles; When the speed of rotation increases as necessary, the power exceeds the maximum, the grinding effect is the best, and the ball …
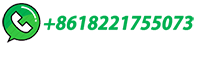