Understanding Die Casting: The Process, Materials, and …
Metal die casting is a precise and efficient process of creating various metal parts. ... The cold chamber casting system is especially valued for its ability to produce large, sturdy parts with exceptional mechanical properties and high durability. ... Vacuum casting differs from traditional casting because it uses a vacuum to prevent air ...
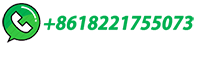